Servo
A servo, short for "servomechanism" or "servomotor," is a specialized type of electro-mechanical device that uses feedback to control and maintain the position, speed, or other parameters of a mechanical system. It consists of a motor, a feedback mechanism, and a controller. The motor in a servo is often a DC motor or a brushless motor, and it is responsible for producing the necessary mechanical movement.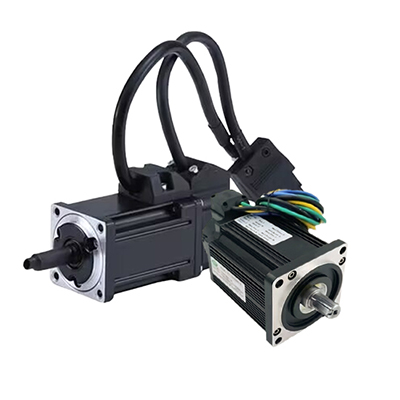
The feedback mechanism in a servo continuously monitors the system's output and provides information to the controller about any deviations from the desired state. The controller then processes this feedback and adjusts the motor's operation to correct the error, bringing the system back to the desired condition.
Servos are widely used in various applications, including robotics, aerospace, automotive systems, and industrial automation. They provide precise and controlled movement, making them essential in scenarios where accuracy and responsiveness are critical. The versatility of servos makes them valuable components in diverse technological fields, contributing to advancements in automation, remote servo control systems, and other areas requiring precise motion control.
|
Rated Power |
Rated Torque |
AC Servo Motor, single phase or three phase 220V DC |
||
1 |
50W AC Servo Motor |
0.16 Nm |
2 |
400W AC Servo Motor |
1.27 Nm |
3 |
750W AC Servo Motor |
2.4 Nm |
4 |
1.5KW AC Servo Motor |
5 Nm |
5 |
2KW AC Servo Motor |
7.7 Nm |
6 |
5.5KW AC Servo Motor |
27 Nm |
DC Servo Motor, brake apparatus 24V DC, brake release when powered |
||
7 |
100W DC Servo Motor |
0.31 Nm |
8 |
200W DC Servo Motor |
1.27 Nm |
9 |
400W DC Servo Motor |
2.25 Nm |
10 |
500W DC Servo Motor |
3 Nm |
11 |
1000W DC Servo Motor |
6.3 Nm |
12 |
1500W DC Servo Motor |
9.5 Nm |
(If need to buy other ATO servo motor, please contact us.)
Servo motor refers to the engine that controls the operation of mechanical components in the servo system. It is an indirect transmission device that assists the motor.
Servo motors can control speed and position accuracy accurately, and can convert voltage signals into torque and rotational speed to drive control objects. Compared with single-machine asynchronous motors, servo motors have three significant characteristics: large starting torque, wide operating range, and no rotation phenomenon.
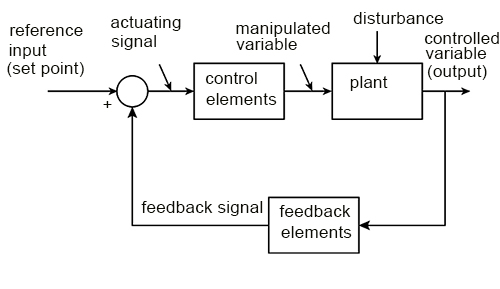
The engine that controls the operation of mechanical components in a servo system is called a servo motor, which is an indirect transmission device that assists the motor. The servo motor converts the voltage signal into two forms: torque and speed to drive the control object. The servo motor can control the speed and its position accuracy is very high.
It mainly relies on pulses for positioning. It is similar to: when the servo motor receives a pulse, it will rotate an angle corresponding to the pulse to achieve displacement; at the same time, it will send a pulse to the servo system. It echoes the pulses received by the servo motor, so that the system will know how many pulses are emitted and retracted, thereby accurately controlling the motor rotation and achieving high-precision positioning.
Motor Performance Curves
The most commonly used motor performance curves are efficiency, speed, power, current in servo, and all of them are plotted as a function of load torque. Both speed and current are linear functions of the load torque TL, as shown in Eg. (1) and Eq. (2). The linear form of both equations is y = mx + b, where the load torque is the independent parameter and the current and speed are the dependent parameters.
Current: I=1/Kt × TL + TM/Kt (1)
Speed: ω=(-Rt/Kt×Ke) × TL + (E/Ke-RtTM/KtKe) (2)
The following picture shows typical performance curves for speed and current. The projection on the shaft represents the theoretical no-load value for an ideal motor without loss of internal torque. Building the curves is a simple process. In both diagrams, the idle and stall points are connected by straight lines. When the load torque changes, the motor will run on this line.
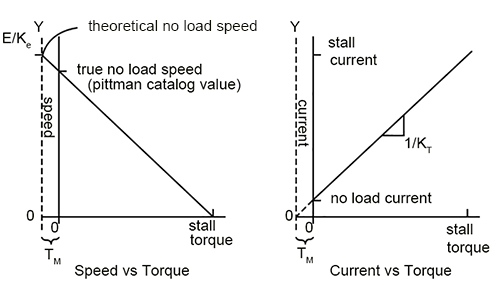
Eg (2) also shows that the motor speed is a function of the applied voltage. Both idle speed and stall torque are proportional to the applied voltage (as long as TM is small). By changing the applied voltage, the motor can operate anywhere in the first quarter of the speed-torque plane. The idle speed and stall torque values in the Pittman catalog are for the nominal winding voltages listed in the catalog. The torque curve is independent of the applied voltage.
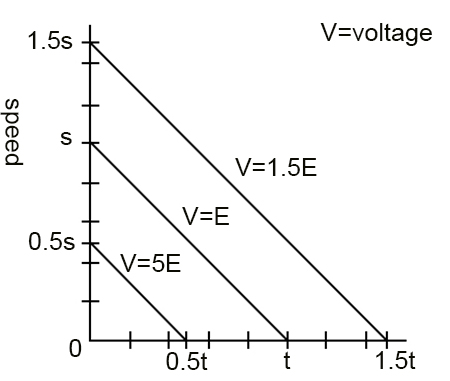
Each technology has its niche, and since the selection of either of these technologies for a given application affects its chance of success, it is important for the machine designer to select the best motor-drive system for the application, while considering the technical advantages and disadvantages of both. It is all about utilizing these technologies with balance to achieve the desired process performance for a given machine design while balancing cost versus the capability of the required mechanism.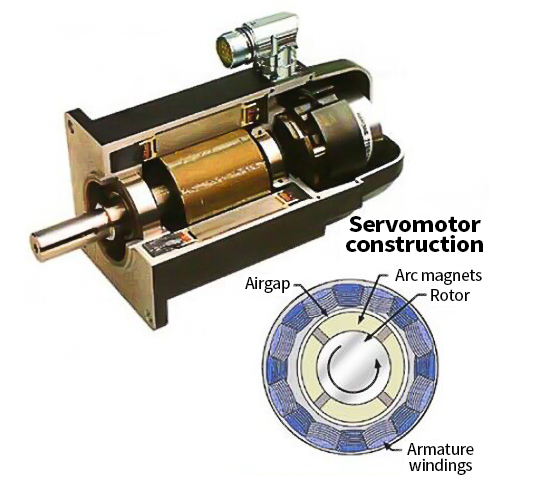
This article presents an overview of different baseline capabilities for selection criteria between stepper and servo technology. A thorough understanding of these technologies will help generate the best and most efficient mechatronic designs to bring forth the full capability of a machine.
Today’s digital stepper motor drives provide enhanced drive features, option flexibility, and communication protocols using advanced integrated circuits and simplified programming techniques. The same is true of servo motor systems, while higher torque density, improved electronics, algorithms, and higher feedback resolution have resulted in higher system Bandwidth (BW) capabilities, and lower initial and overall operating costs for many applications.
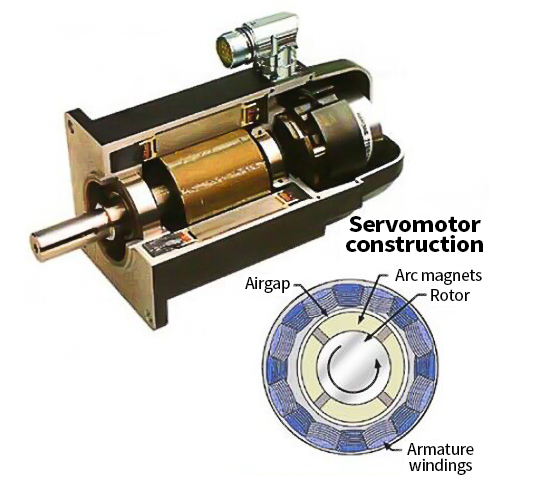
This article presents an overview of different baseline capabilities for selection criteria between stepper and servo technology. A thorough understanding of these technologies will help generate the best and most efficient mechatronic designs to bring forth the full capability of a machine.
Today’s digital stepper motor drives provide enhanced drive features, option flexibility, and communication protocols using advanced integrated circuits and simplified programming techniques. The same is true of servo motor systems, while higher torque density, improved electronics, algorithms, and higher feedback resolution have resulted in higher system Bandwidth (BW) capabilities, and lower initial and overall operating costs for many applications.
A servo is a mechanical motorized device that can be instructed to move the output shaft attached to a servo wheel or arm to a specified position. Inside the servo box is a DC motor mechanically linked to a position feedback potentiometer, gearbox, electronic feedback control loop circuitry and motor drive electronic circuit. A typical RC servo looks like a plastic rectangular box with a rotary shaft coming up and out the top of the box and three electrical wires out of the servo side to a plastic 3 pin connector. Attached to the output shaft out the top of the box is a servo wheel or Arm. These wheels or arms are usually a plastic part with holes in it for attaching push / pull rods, ball joints or other mechanical linkage devices to the servo. The three electrical connection wires out of the side are V- (Ground), V+ (Plus voltage) and S Control (Signal). The control S (Signal) wire receives Pulse Width Modulation (PWM) signals sent from an external controller and is converted by the servo on board circuitry to operate the servo.
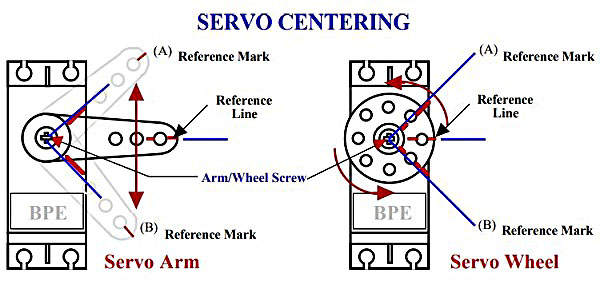
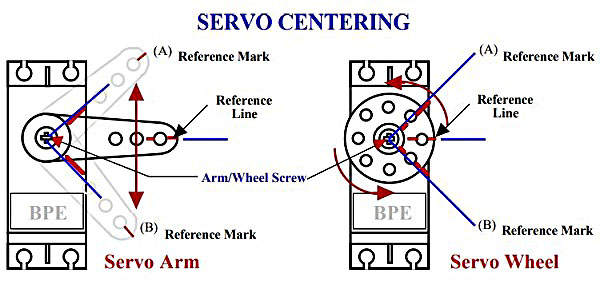
The importance of servo motor sizing should not be underestimated. Proper motor sizing will
not only result in significant cost savings by saving energy, reducing purchasing and operating costs, reducing downtime, etc.; it also helps the engineer to design better motion control systems. The servo motor represents the most influential cost factor in the motion control system design, not only during the purchasing process, but especially during servo operation. A high-torque motor will require a stronger and thus more expensive amplifier than smaller motors. The combination of higher torque motor plus amplifier results not only in higher initial expenses, but will also lead to higher operational costs, in particular increased energy consumption. It is estimated, that the purchase price represents only about 2% of the total life cycle costs; about 96% is electricity.
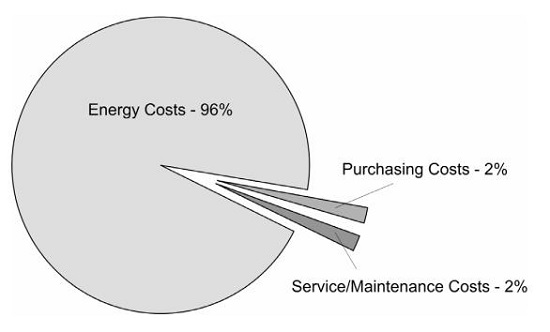
AC servo motor is a very important part of the AC servo system. AC servo motors play a key role in automation systems, so correct installation is critical to system performance and stability. Please observe the installation instructions described below to install the servo motor correctly.
Servomotors can be mounted horizontally with the motor shaft oriented in the same direction as the machine shaft. When mounting an AC servo motor, the direction of the motor shaft should be the same as the direction of the mechanical shaft. This is to ensure that the motor operates properly and does not cause problems such as stalling or abnormal wear. If the direction of the motor shaft is not consistent with the direction of the mechanical shaft, it may lead to a mismatch between the motor and the mechanical load, affecting the performance and life of the motor.
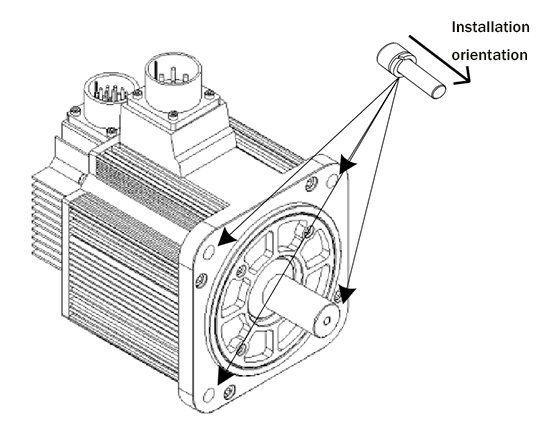
A servo control system is an electronic control system that realizes precise position and speed control.
Servo control systems can be categorized into several types based on different classification criteria. Such as motor servo control system is the most common type of servo control system, which realizes precise control of objects by controlling the speed, steering and position of the motor. Motor servo control systems are widely used in industrial automation fields, such as CNC machine tools, elevators, etc.
Servo control systems can be classified according to the control mode, control object and control method. Different types of servo control systems have a wide range of applications in different application areas. With the continuous progress of science and technology, the servo control system will play an important role in more fields, bringing more convenience and benefits to people's production and life.
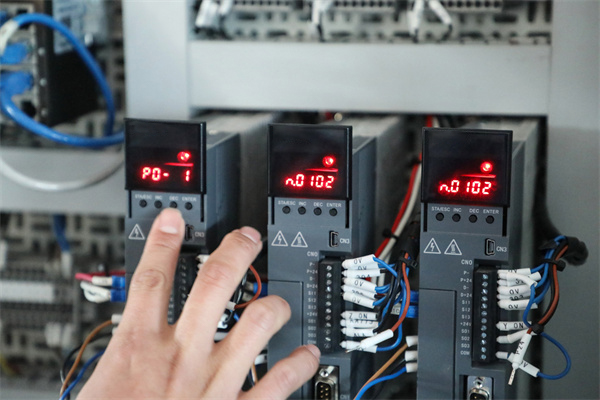
Servo control systems can be classified according to the control mode, control object and control method. Different types of servo control systems have a wide range of applications in different application areas. With the continuous progress of science and technology, the servo control system will play an important role in more fields, bringing more convenience and benefits to people's production and life.
Today we will learn to control a servomotor. We'll use a continuous rotation servo, which makes our servo motor rock-and-roll. The control procedure that we will learn is also applicable to any servo motor.
The external controller controls the servo system through a signal called PPM code modulation to avoid confusion with pulse width modulation. A control wire communicates the desired angular movement to the servo. The angle is determined by the duration of the pulse applied to the control wire.
PPM uses 1 to 2ms out of a 20ms time period to encode its information. The servo expects to see a pulse every 20 milliseconds (02 seconds). The length of the pulse will determine how far the motor turns. A 1.5-millisecond pulse will make the motor turn to the 90-degree position (often called the neutral position). If the pulse is shorter than 1.5ms, then the motor will turn the shaft closer to 0 degrees. If the pulse is longer than 1.5ms, the shaft turns closer to 180 degrees.
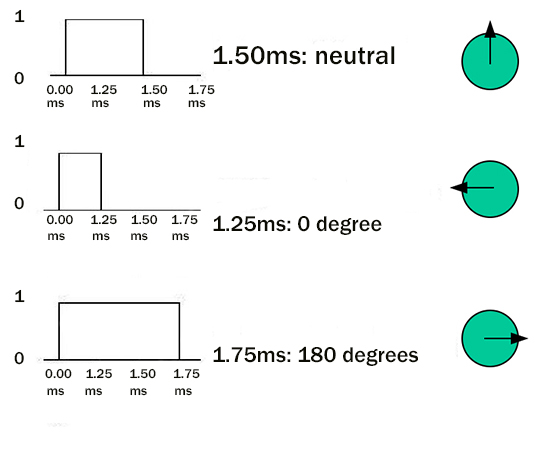
The external controller controls the servo system through a signal called PPM code modulation to avoid confusion with pulse width modulation. A control wire communicates the desired angular movement to the servo. The angle is determined by the duration of the pulse applied to the control wire.
PPM uses 1 to 2ms out of a 20ms time period to encode its information. The servo expects to see a pulse every 20 milliseconds (02 seconds). The length of the pulse will determine how far the motor turns. A 1.5-millisecond pulse will make the motor turn to the 90-degree position (often called the neutral position). If the pulse is shorter than 1.5ms, then the motor will turn the shaft closer to 0 degrees. If the pulse is longer than 1.5ms, the shaft turns closer to 180 degrees.
DC servo motor refers specifically to DC brushed servo motor - the servo motor has low cost, simple structure, large starting torque, wide speed range, easy control, requires maintenance, but is easy to maintain (replace carbon brushes). DC servo motors have good starting, braking and speed regulation characteristics, and can easily achieve smooth speed regulation in a wide range. Therefore, they are often used in production equipment that requires high speed regulation performance of servo motors.
DC motor component
DC servo motor is mainly composed of stator, rotor core, motor shaft, servo motor winding commutator, servo motor winding, speed measuring motor winding, speed measuring motor commutator and other components.DC servo motor constructure.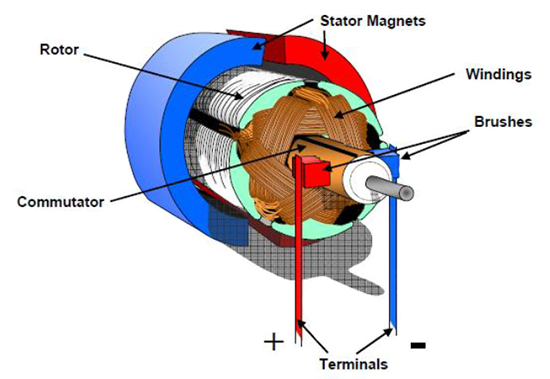
DC motor component
DC servo motor is mainly composed of stator, rotor core, motor shaft, servo motor winding commutator, servo motor winding, speed measuring motor winding, speed measuring motor commutator and other components.DC servo motor constructure.
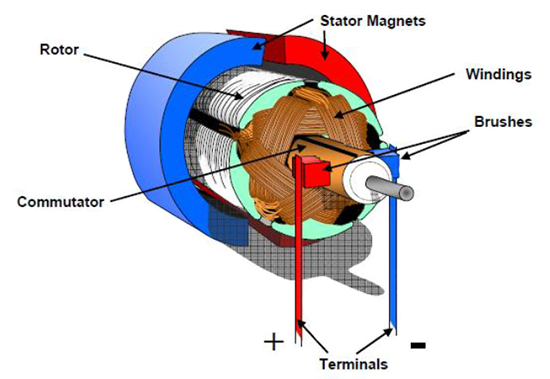
- Stator. Stator pole magnetic field is generated by the magnetic poles of the stator. According to the way of generating magnetic field, DC servo motors can be divided into permanent magnet type and separately excited type. The permanent magnetic poles are made of permanent magnet materials, and the separately excited magnetic poles are made of laminated stamped silicon steel sheets. The external coil is passed through a DC current to generate a constant magnetic field.
- Rotor. Also known as the armature, it is made of laminated silicon steel sheets with coils embedded on the surface. When DC current is passed, the electromagnetic torque that drives the load to rotate is generated under the action of the stator's magnetic field.
- Brushes and commutator segments. In order to keep the generated electromagnetic torque in a constant direction, the rotor can rotate uniformly and continuously in a fixed direction, the brushes are connected to the external DC power supply, and the commutator segments are connected to the armature conductors.
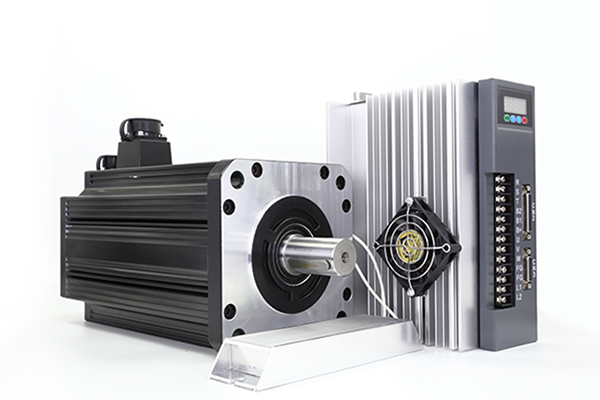
Category
Featured Articles
What is a Servo Motor?
There are some special types of application of electrical motor where rotation of the motor is required for just a certain angle ...
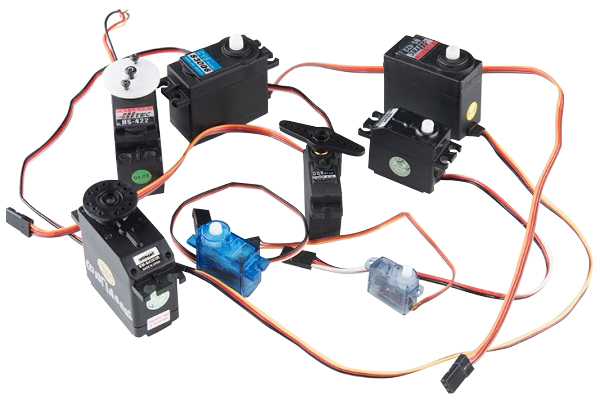
What are the Basics of Servo Drive?
Servo motors come in so many types and flavors that it is difficult to define them in a way that is accurate and universally ...
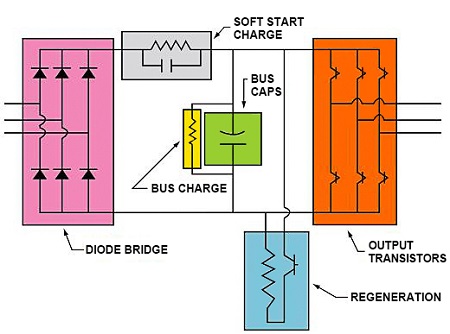
Why Use Servo Motor as Test Load?
Dynamometer is mainly divided into two parts: cabinet and frame, while the frame mainly has the motor under test, torque speed ...
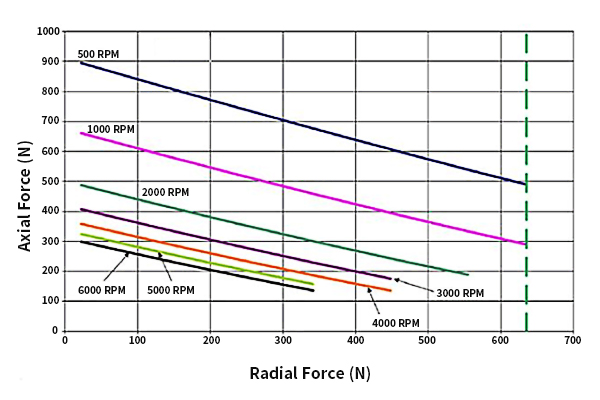
What Should Consider Before Using ...
Servo system is a commonly used control system, widely used in industrial automation. It compares the output signal with the ...
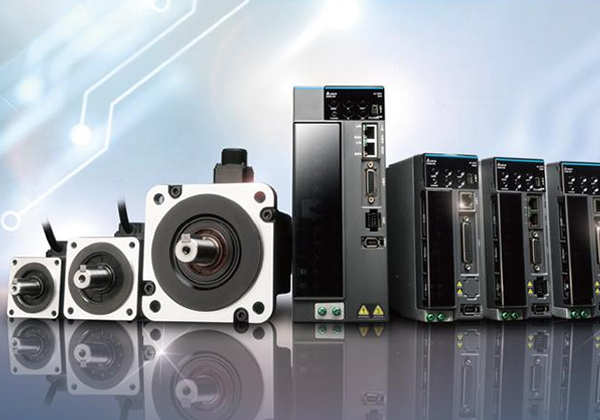
Servo Motor in Food Industry
In the ever-evolving landscape of the food industry, technological advancements play a pivotal role in enhancing efficiency, ...
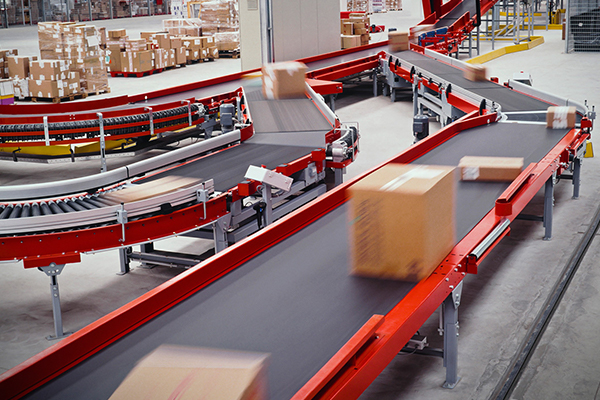