Home » Servo System
When closed-loop hydraulic control systems first began to appear in industry, the applications were generally those in which very high performance was required. While hydraulic servo systems are still heavily used in high-performance applications such as the machine-tool industry, they are beginning to gain wide acceptance in a variety of industries. Examples are material handling, mobile equipment, plastics, steel plants, mining, oil exploration, and automotive testing. Closed loop servo drive technology is increasingly becoming the norm in machine automation, where the operators are demanding greater precision, faster operation, and simpler adjustment. There is also an expectation that the price of increasing the level of automation should be contained within acceptable limits.
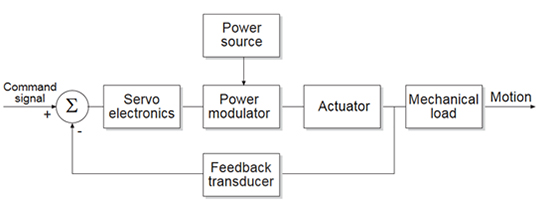
Hydraulic cylinder test and detection is animportant means to guarantee the normal work of the hydraulic system. Due tothe traditional hydraulic cylinder test bed has the problem of low accuracy andlow working efficiency, therefore, an accurate detection and intelligenthydraulic cylinder test-bed is the developing direction in the future.
The hydraulic cylinder test bed adopts theservo control system, using industrial computer as the upper machine,responsible for analog acquisition, data storage; using the PLC as lowermachine, responsible for the control of the action logic of hydraulic components; also used touch screen as the auxiliary equipment. The servo systemimproved the system accuracy, automation and system stability.
The hydraulic cylinder test bed adopts theservo control system, using industrial computer as the upper machine,responsible for analog acquisition, data storage; using the PLC as lowermachine, responsible for the control of the action logic of hydraulic components; also used touch screen as the auxiliary equipment. The servo systemimproved the system accuracy, automation and system stability.
To meet the requirements of extreme accuracy and stability in the repeater design, the obvious choice is an AC system with synchro data transmission. DC compensating networks are discarded because of drift in the associated modulators and demodulators. The form of compensation chosen for this application after a complete study of the requirements was the viscous-couple dinertia damper.
Servo system resonance frequency refers to the frequency at which a resonance phenomenon occurs within the system when it is excited by the outside world in a servo system. In a servo system, resonant frequency is a very important parameter, which directly affects the stability and performance of the system.
Introduction
The Antiaircraft Fire-Control System employs electrical servos for driving the tracking-radar antenna in azimuth and elevation while tracking a target. Only the elevation control channel is illustrated since both channels are identical except that the azimuth power servo amplifier drives four motors. In contrast, the elevation servo amplifier drives a single motor. The units shown are those used in the automatic-tracking mode.
The Antiaircraft Fire-Control System employs electrical servos for driving the tracking-radar antenna in azimuth and elevation while tracking a target. Only the elevation control channel is illustrated since both channels are identical except that the azimuth power servo amplifier drives four motors. In contrast, the elevation servo amplifier drives a single motor. The units shown are those used in the automatic-tracking mode.
In the field of industrial automation, servo control is an important motion control method. S-curve acceleration and deceleration is a commonly used motion control curve in servo system. In this paper, we will discuss the principle of S-curve acceleration and deceleration in servo control and the method of PLC implementation, in order to help readers better understand and apply this technology.
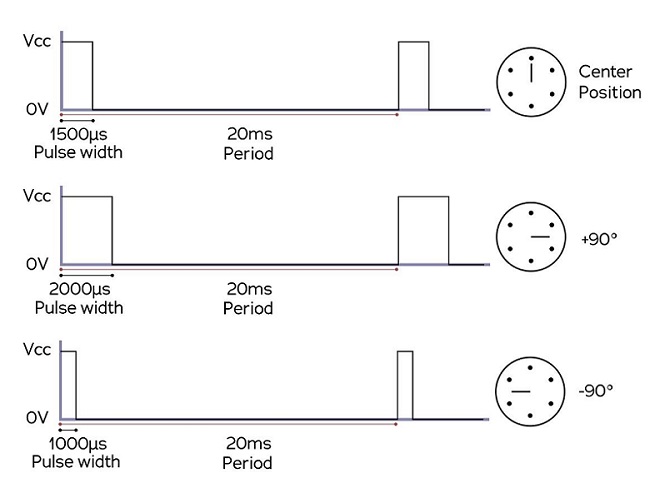
A servo control system is used to precisely follow or reproduce a process. It is an operating system that can automatically control the mechanical movement of a test device according to predetermined requirements. In many cases, the servo system refers exclusively to a feedback control system in which the controlled quantity is a mechanical displacement or displacement velocity or acceleration, and its function is to make the output mechanical displacement accurately follow the input displacement.
Servo system is a commonly used control system, widely used in industrial automation. It compares the output signal with the given reference input signal by means of feedback control, and makes the output signal of the system consistent with the reference input signal by adjusting the output of the controller. After we know what a servo system is, when using the servo system, we need to master some skills to ensure its stable and reliable work.
Proper selection of the type of controller for a servo system is critical. Common servo system controllers include proportional, integral and differential controllers, as well as their combination forms. For different application scenarios, we need to choose the most suitable controller type according to the dynamic characteristics and control requirements of the system. Proportional controllers are suitable for fast response systems, integral controllers are suitable for eliminating steady state errors, and differential controllers are suitable for suppressing system oscillations. When choosing the controller type, it is important to weigh the actual requirements of the system in order to achieve the best control results.
Proper selection of the type of controller for a servo system is critical. Common servo system controllers include proportional, integral and differential controllers, as well as their combination forms. For different application scenarios, we need to choose the most suitable controller type according to the dynamic characteristics and control requirements of the system. Proportional controllers are suitable for fast response systems, integral controllers are suitable for eliminating steady state errors, and differential controllers are suitable for suppressing system oscillations. When choosing the controller type, it is important to weigh the actual requirements of the system in order to achieve the best control results.
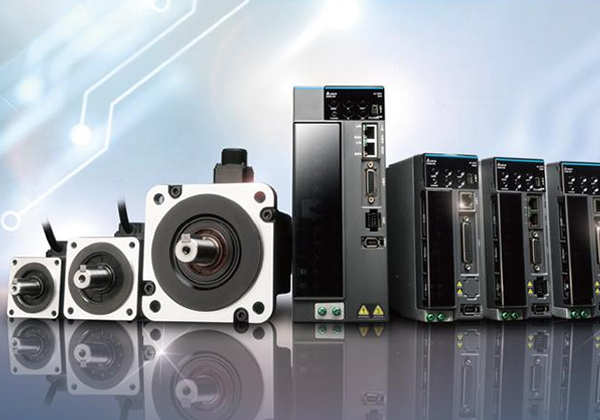
For a servo system, the bandwidth is the maximum sine wave frequency to which the servo system can respond. In professional terms, it is the frequency at which the amplitude response decays to -3dB, or the frequency at which the phase response lags by 90 degrees. A servo is also a signaling system and can be thought of as a low-pass filter. It always lets the lower frequency components through and attenuates the higher frequency parts. Therefore, the wider the bandwidth, the better the servo system's output can follow the input commands, and the better the system's dynamic performance.
Both hobbyists and industrial companies use "servos", but they are quite different in their components and applications. We use both extensively, depending on the best fit for the project. Hobby vehicles move mass in a very unorganized fashion, and need to carry their own energy source on board. Mostly this means a battery pack of some sort, and this (along with other consumer electronics) has driven a large change in battery technology. The latest batteries that have a relatively high energy density is the Lithium Polymer battery, a cousin of the much safer Lithium-Ion battery found in nearly every portable device we power with rechargeable batteries.
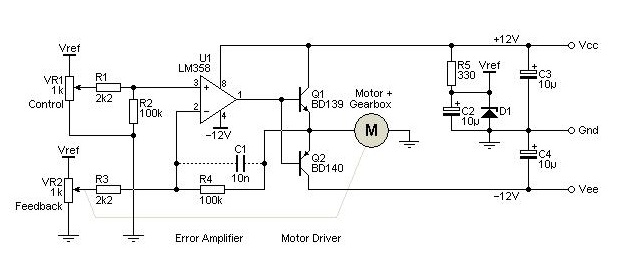
A servo system is a critical component in various applications, ranging from robotics and manufacturing to aerospace and automotive industries. It plays a crucial role in providing precise control of position, velocity, and acceleration of mechanical systems. To ensure optimal performance, several technical requirements must be considered in the design and implementation of a servo system.
Such as servo system accuracy refers to the degree of precision with which the output volume reproduces the input signal requirements, expressed in the form of error, i.e., dynamic error, steady state error, and static error. Stabilized servo system to the input changes are reflected in the form of an oscillation decay, the amplitude and process of oscillation produces the dynamic error of the system. When the system oscillation decay to a certain degree, we call it steady state, the system error is the steady state error. The error determined by the accuracy of the device's own parts and assembly accuracy is usually referred to as the static error.
Such as servo system accuracy refers to the degree of precision with which the output volume reproduces the input signal requirements, expressed in the form of error, i.e., dynamic error, steady state error, and static error. Stabilized servo system to the input changes are reflected in the form of an oscillation decay, the amplitude and process of oscillation produces the dynamic error of the system. When the system oscillation decay to a certain degree, we call it steady state, the system error is the steady state error. The error determined by the accuracy of the device's own parts and assembly accuracy is usually referred to as the static error.
Servomechanisms, called servos for short, are the basic building blocks of power drives. In this manual what we mean by a power drive is an electric or electrohydraulic machine which positions a launcher or other device in accordance with a relatively weak electrical signal. We will consider a power drive as a big servo made up of smaller ones. Not only is feedback important in understanding servos, but it also has important applications in the electronic and hydraulic fields. Therefore, if you know how feedback is used in servos, you can better understand how it is used in electronics and hydraulics.
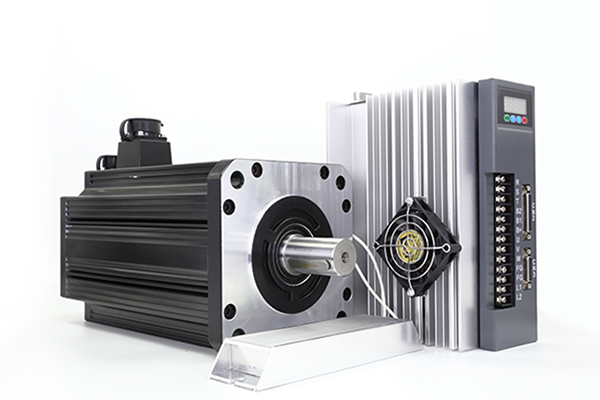
Category
Featured Articles
What Should Consider Before Using ...
Servo system is a commonly used control system, widely used in industrial automation. It compares the output signal with the ...
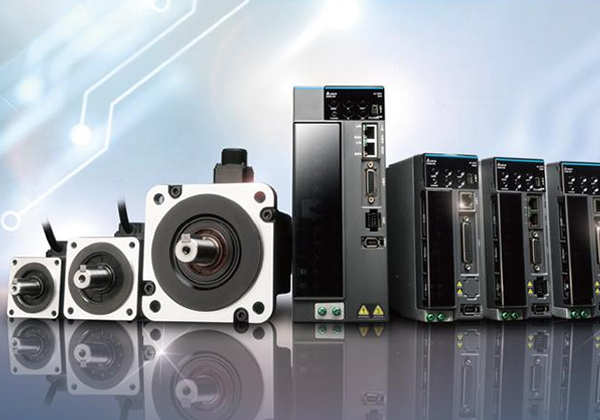
What is the Bandwidth of ...
For a servo system, the bandwidth is the maximum sine wave frequency to which the servo system can respond. In professional ...
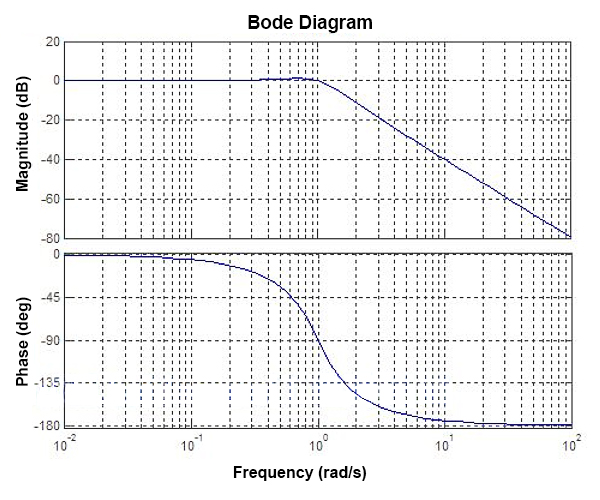
What are the Basic Components of ...
Servomechanisms, called servos for short, are the basic building blocks of power drives. In this manual what we mean by a power ...
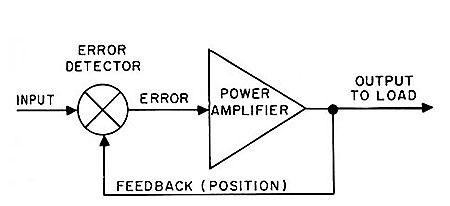
What is Servo System?
A feedback control system used to precisely follow or reproduce a process. Also known as a follower system. In many cases, a ...
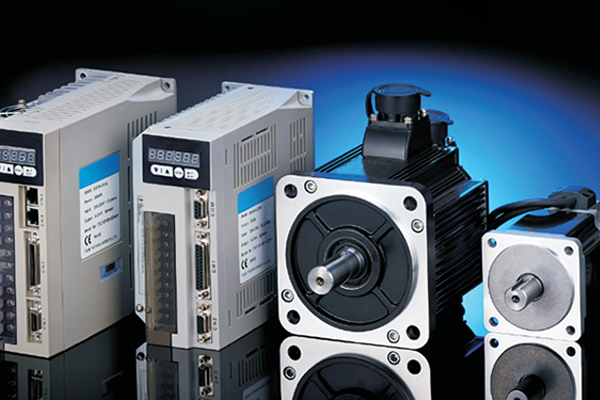