Home » Wiki
Servo motors and VFDs are typicallycomprised of two parts - the motor itself and a controller (also called"amplifier," "servo pack" or "inverter”) which drivesthe motor and is connected to it by cable. The controller receives power fromAC mains: a single phase for low-to-medium power drives and three phases forhigh-power drives. A typical manufacturing and robotic tool may have as littleas one and as many as 20 such drives. Servo motors have a feedback circuit thatallows them to maintain specific positions with high accuracy. This also meansthat servo motors work even when they are not moving. Variable frequency drives(VFD) work differently - their speed is controlled by the frequency of thedrive signal. What is common between these two different types of drives isthat both are driven by pulsed signals.
What is commutation and how does it affect the performance of the linear motors? Commutation is the process of switching current in the phases in order to generate motion. Most linear motor designs use a three-phase brushless design. In brushed motors, commutation is easy to understand as brushes contact a commutator and switch the current as the motor moves. Brushless technology has no moving contacting parts and therefore is more reliable. However, the electronics required to control the current in the motor are a little more complex. The method of communication depends on the application of the motor, but it is important to understand how the motor can be communicated and what disadvantages some method shave.
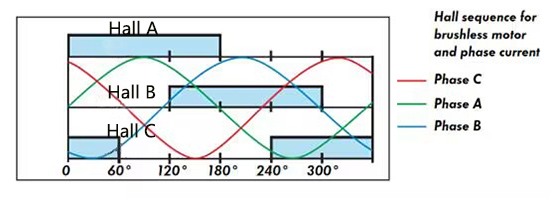
This paper is intended to allow a user to fully understand the Servo Cylinder Test Sheet results, and how to apply these results to better understand your actuator. Testing on Servo Cylinder actuators is conducted in a specialized fixture, which is equipped with a load force supplying actuator, an external optical strip encoder, and a load cell. All other measurements such as encoder position and torque feedback come from the built in drive electronics. Some tests require no outside loading or measurements. These unloaded tests are conducted in a decoupled state, and do not require the fixture.
Tests procedures that are performed on a Servo Cylinder actuator can be divided into two groups, tests that can be run with only the on board drive electronics, and tests that require external loads and measurements, which are supplied by a custom test fixture. These tests are respectively referred to as unloaded and loaded tests, and on an actuator's test sheet.
Tests procedures that are performed on a Servo Cylinder actuator can be divided into two groups, tests that can be run with only the on board drive electronics, and tests that require external loads and measurements, which are supplied by a custom test fixture. These tests are respectively referred to as unloaded and loaded tests, and on an actuator's test sheet.
Servo motor is a kind of motor that can precisely control the speed and position, which is widely used in the field of mechanical equipment and industrial automation. The design process of servo motor needs to go through several steps, this article will introduce the specific steps of servo motor design in detail.
A servo motor is a type of motor that can realize precise position control based on input control signals. It can precisely control the position of the motor by controlling the motor's speed and steering so that it stops at the specified position. The positioning principle of a servo motor involves several important technical points, which will be introduced one by one in this article.
Servo torque accuracy refers to the torque control accuracy of the servo system in the working process. The level of torque accuracy directly affects the stability and control accuracy of the servo system. In many applications that require precise torque control, such as robotics, CNC machine tools and other fields, servo torque accuracy is an important technical indicator.
Servo motors are critical components in various industrial applications, ranging from robotics to manufacturing processes. One key parameter that significantly influences the performance of a servo motor is the number of poles.
The number of motor pole pairs of a servo motor is the number of poles required to turn the motor one revolution. Simply put, it is one of the parameters used to characterize a servo motor. The motor pole pair number affects the operation speed, precision, stability and other aspects of the motor. So, how do we understand the electric servo motor motor pole pair number? The following will be introduced in steps.
The size and number of poles and windings in a motor have a significant impact on the performance of the motor. The number of motor pole pairs refers to the number of magnetic poles required for one revolution of the motor. The more the number of motor pole pairs, the slower the motor's movement speed, but the higher the precision and stability; on the contrary, the less the number of motor pole pairs, the faster the movement speed, but the precision and stability of the motor's movement is a little worse.
The number of motor pole pairs of a servo motor is the number of poles required to turn the motor one revolution. Simply put, it is one of the parameters used to characterize a servo motor. The motor pole pair number affects the operation speed, precision, stability and other aspects of the motor. So, how do we understand the electric servo motor motor pole pair number? The following will be introduced in steps.
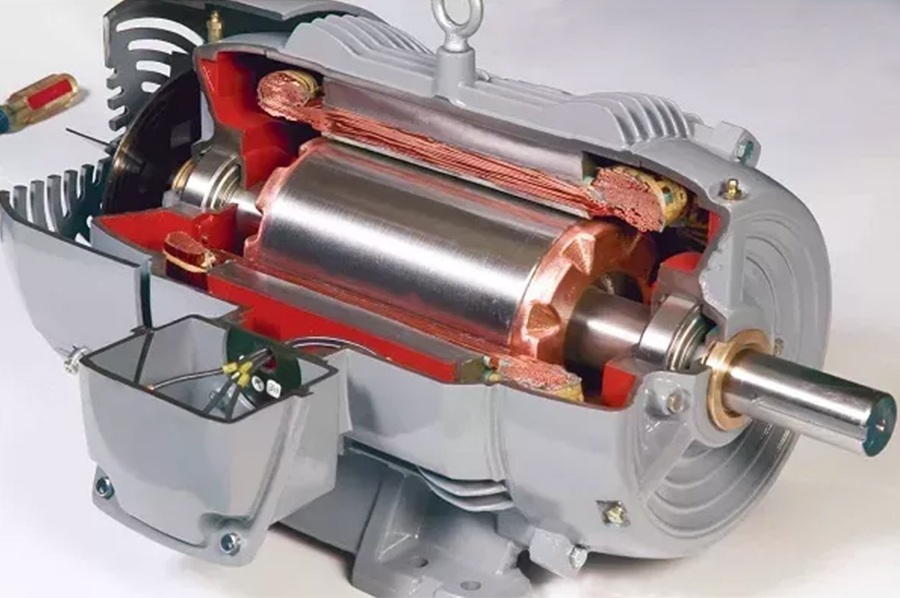
The size and number of poles and windings in a motor have a significant impact on the performance of the motor. The number of motor pole pairs refers to the number of magnetic poles required for one revolution of the motor. The more the number of motor pole pairs, the slower the motor's movement speed, but the higher the precision and stability; on the contrary, the less the number of motor pole pairs, the faster the movement speed, but the precision and stability of the motor's movement is a little worse.
This work is focused on the analysis of the so-called accelerating factor (α) defined, for each motor, as the ratio between the square of the motor nominal torque and its momentum of inertia.
The need to increase production capability, while maintaining the quality standards, requires the implementation of automatic machines performance ever higher. In this context, it is of strategic importance in the machine design phase the correct selection of the motor reducer unit. Unfortunately, the choice of the electric motor required to handle a dynamic load, is closely related to the transmission choice. This operation, in fact, is bound by the limitations imposed by the motor working range and it is subjected to a great number of constraints that depend indirectly on the motor (through its inertia) and on the reducer, whose selection is the object of the design. This work is focused on the analysis of the "continuous duty power rate" also called "accelerating factor" defined, for each motor, as the ratio between the square of the motor nominal torque and its momentum of inertia.
The need to increase production capability, while maintaining the quality standards, requires the implementation of automatic machines performance ever higher. In this context, it is of strategic importance in the machine design phase the correct selection of the motor reducer unit. Unfortunately, the choice of the electric motor required to handle a dynamic load, is closely related to the transmission choice. This operation, in fact, is bound by the limitations imposed by the motor working range and it is subjected to a great number of constraints that depend indirectly on the motor (through its inertia) and on the reducer, whose selection is the object of the design. This work is focused on the analysis of the "continuous duty power rate" also called "accelerating factor" defined, for each motor, as the ratio between the square of the motor nominal torque and its momentum of inertia.
The rotor inertia of a servo motor is a very important parameter in the design and use of motors, which is directly related to the control performance and responsiveness of the motor. In this article, the definition, calculation method, influencing factors and optimization method of rotor inertia of servo motor will be introduced in detail.
The rotor inertia of a servomotor refers to the inherent moment of inertia of the motor rotor, which indicates the inertia characteristics of the motor for speed changes. Generally speaking, the larger the rotor inertia is, the worse the response performance of the motor is and the more difficult it is to control.
A variety of methods can be used to calculate the rotor inertia of a servomotor, and some of the more commonly used methods include the dynamic and static methods.
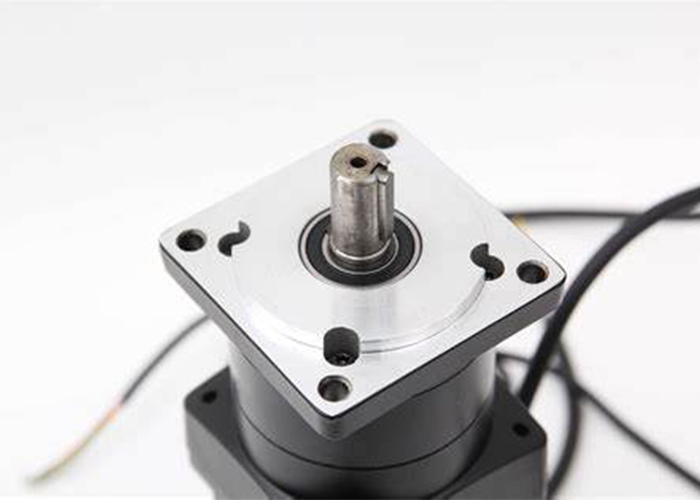
The rotor inertia of a servomotor refers to the inherent moment of inertia of the motor rotor, which indicates the inertia characteristics of the motor for speed changes. Generally speaking, the larger the rotor inertia is, the worse the response performance of the motor is and the more difficult it is to control.
A variety of methods can be used to calculate the rotor inertia of a servomotor, and some of the more commonly used methods include the dynamic and static methods.
As a kind of high-performance motor equipment, servo motor is widely used in industrial automation control system. The insulation level of servo motor refers to the voltage resistance of its insulating material, which is one of the important indexes to judge the safety and reliability of servo motor. In this article, the definition, test standard and application of servo motor insulation level will be introduced in detail.
The zero return point of a servo motor is a specific point at which the servo motor returns to its initial position during motion. The determination of the zero return point is very important for the normal operation and precise contr
ol of the servo motor. This article will introduce the significance of the zero return point, the method of determining the zero return point and the application of the zero return point.
Return-to-zero is a key concept in servo motor motion control that determines the initial position of the motor. In many applications, servo motors need to return to the initial position periodically to ensure accurate position control and motion control. By setting the zero return point, the motor can be made to return to the same starting position after each startup or repositioning for stable motion control.
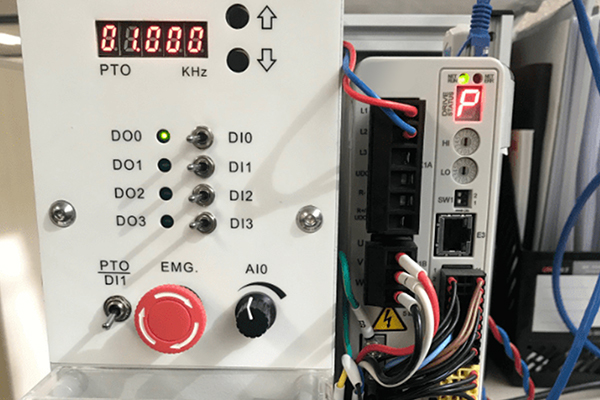
Return-to-zero is a key concept in servo motor motion control that determines the initial position of the motor. In many applications, servo motors need to return to the initial position periodically to ensure accurate position control and motion control. By setting the zero return point, the motor can be made to return to the same starting position after each startup or repositioning for stable motion control.
Dynamometer is mainly divided into two parts: cabinet and frame, while the frame mainly has the motor under test, torque speed sensor, mechanical load. Currently, servo motors are mostly used as loads. Servo motors convert electrical signals into torque and speed to drive the control object. Servo motor rotor speed is controlled by the input signal, and can respond quickly, in the automatic control system, used as an executive element, and has a small electromechanical time constant, high linearity, starting voltage and other characteristics.
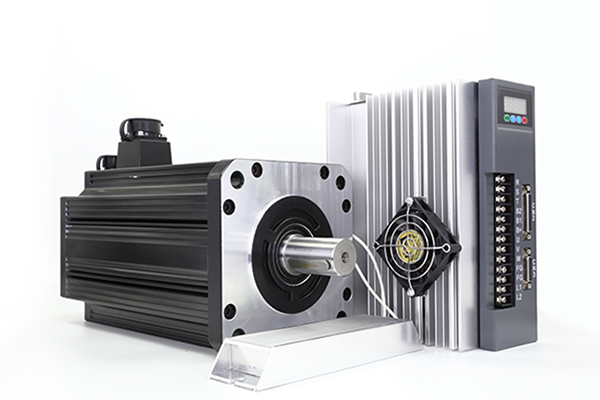
Category
Featured Articles
Why Use Servo Motor as Test Load?
Dynamometer is mainly divided into two parts: cabinet and frame, while the frame mainly has the motor under test, torque speed ...
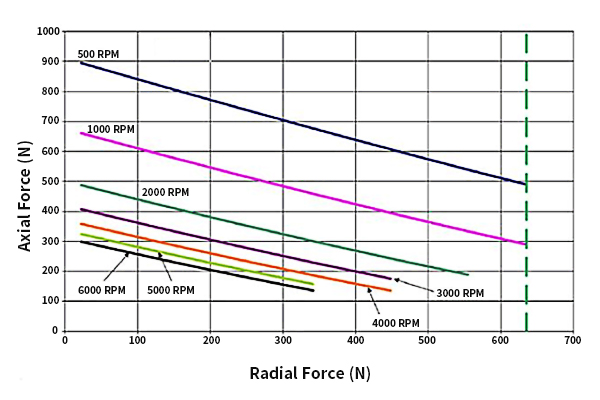
Troubleshooting of Servo Motor
Servo motors play a crucial role in various industrial applications, providing precision control and efficient performance. ...
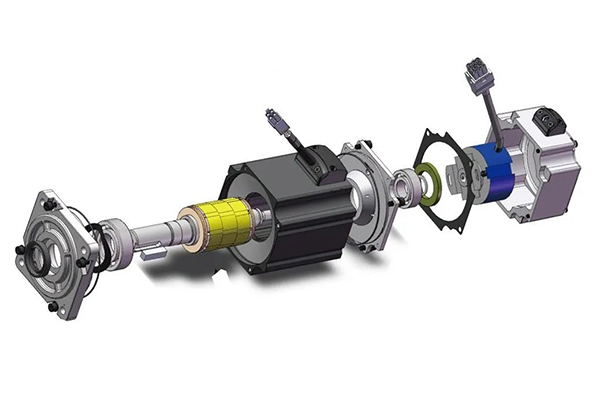
Difference Between Servo and Stepper ...
Servo motor and stepper motor are almost used in all automated industries where high precision is to be achieved. Though servo ...
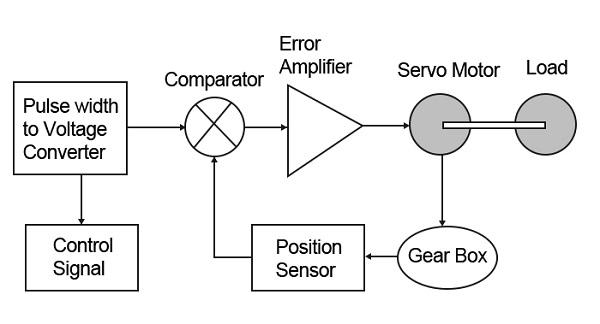
Safety Precaution For Using Servo Motor
In the realm of industrial automation, servo motors play a crucial role in achieving precision and control. These devices are ...
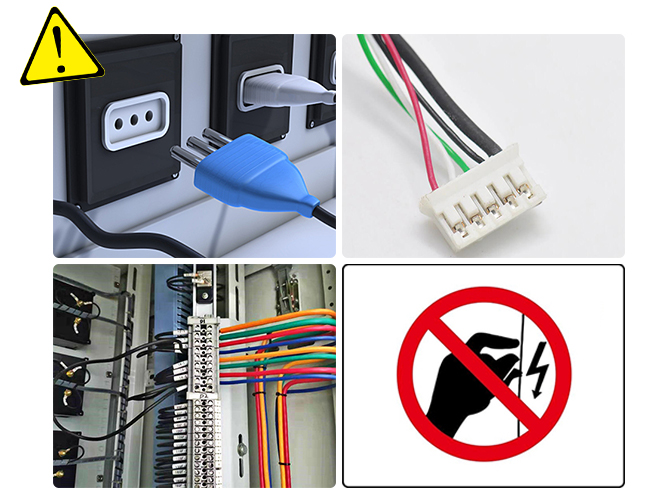