Servo Motor Rotor Inertia: Calculation Method and Influencing Factor
The rotor inertia of a servo motor is a very important parameter in the design and use of motors, which is directly related to the control performance and responsiveness of the motor. In this article, the definition, calculation method, influencing factors and optimization method of rotor inertia of servo motor will be introduced in detail.
Definition:
The rotor inertia of a servomotor refers to the inherent moment of inertia of the motor rotor, which indicates the inertia characteristics of the motor for speed changes. Generally speaking, the larger the rotor inertia is, the worse the response performance of the motor is and the more difficult it is to control.
Calculation Method:
A variety of methods can be used to calculate the rotor inertia of a servomotor, and some of the more commonly used methods include the dynamic and static methods.
1. Dynamic Method
The idea of the dynamic method to calculate the rotor inertia is to accelerate the motor to a certain speed, and then stop the power, record the time and acceleration of the motor to continue to rotate after the power is stopped, and then the kinematic equations can be used to derive the moment of inertia of the motor rotor.
The equation is as follows:
J = τ / α
Where J is the rotor inertia, τ is the torque of the motor that continues to rotate after power failure, and α is the acceleration of the motor that continues to rotate after power failure.
2. Static Method
The idea of the static method to calculate the rotor inertia is to rotate the motor to a certain speed, and then apply a certain size of torque, record the acceleration and acceleration time of the motor, and the moment of inertia of the rotor of the motor can be derived through Newton's second law.
The formula is as follows:
J = T / (ω2 - ω1)
where J is the rotor inertia, T is the applied torque, and ω1 and ω2 are the motor starting and ending speeds, respectively.
Influencing Factors
The size of the rotor inertia of the industrial servo motor is affected by a variety of factors, mainly including motor structure, materials, quality and operating conditions and other factors.
In order to optimize the rotor inertia of the servo motor, the following methods can be used:
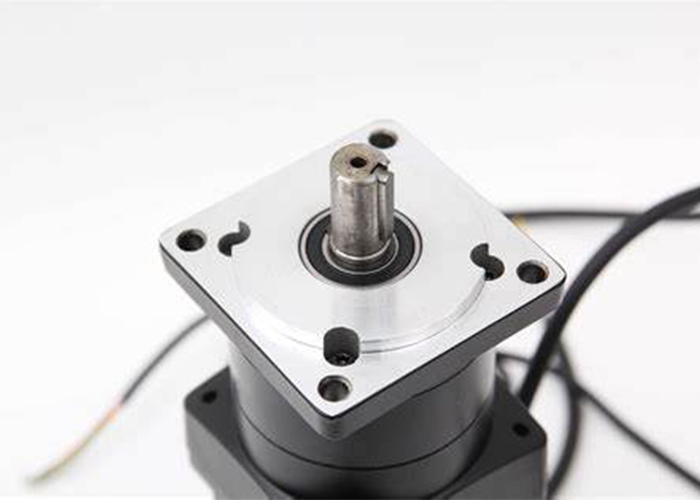
Definition:
The rotor inertia of a servomotor refers to the inherent moment of inertia of the motor rotor, which indicates the inertia characteristics of the motor for speed changes. Generally speaking, the larger the rotor inertia is, the worse the response performance of the motor is and the more difficult it is to control.
Calculation Method:
A variety of methods can be used to calculate the rotor inertia of a servomotor, and some of the more commonly used methods include the dynamic and static methods.
1. Dynamic Method
The idea of the dynamic method to calculate the rotor inertia is to accelerate the motor to a certain speed, and then stop the power, record the time and acceleration of the motor to continue to rotate after the power is stopped, and then the kinematic equations can be used to derive the moment of inertia of the motor rotor.
The equation is as follows:
J = τ / α
Where J is the rotor inertia, τ is the torque of the motor that continues to rotate after power failure, and α is the acceleration of the motor that continues to rotate after power failure.
2. Static Method
The idea of the static method to calculate the rotor inertia is to rotate the motor to a certain speed, and then apply a certain size of torque, record the acceleration and acceleration time of the motor, and the moment of inertia of the rotor of the motor can be derived through Newton's second law.
The formula is as follows:
J = T / (ω2 - ω1)
where J is the rotor inertia, T is the applied torque, and ω1 and ω2 are the motor starting and ending speeds, respectively.
Influencing Factors
The size of the rotor inertia of the industrial servo motor is affected by a variety of factors, mainly including motor structure, materials, quality and operating conditions and other factors.
- Structure. The complexity of the motor structure, the shape of the stator and rotor, the positioning method and other factors will affect the size of the servomotor rotor inertia. Generally speaking, the closer the moments of inertia of the stator and rotor are, the smaller the motor rotor inertia will be.
- Material. The material of the motor rotor also affects its moment of inertia. Generally speaking, the larger the mass of the material, the larger the rotor inertia. At the same time, the material's modulus of elasticity, coefficient of thermal expansion and other physical characteristics will also have an impact on the motor rotor inertia.
- Mass. The mass of the motor rotor is also an important factor affecting its moment of inertia. In addition to the size of the mass itself, the distribution of the mass is also important. If the mass of the motor rotor is not evenly distributed, the rotor inertia will also increase.
- Operating condition. The operating condition of the motor also has an effect on its rotor inertia. The rotor inertia of the motor may also vary under different operating conditions.
In order to optimize the rotor inertia of the servo motor, the following methods can be used:
- Optimization of materials. The use of light weight and high strength materials can effectively reduce the moment of inertia of the motor rotor and improve the corresponding capacity of the motor.
- Optimizing structure. The moment of inertia of the motor rotor can be reduced by optimizing the motor structure and reducing the rotor mass.
- Control algorithm. Optimized control algorithm can control the response speed and stability of the motor better. Advanced control methods, such as fuzzy control, neural network control, etc., can achieve better control results.
- Reduce load inertia. Through the use of speed reducers, clutches and other devices, the load inertia can be effectively reduced, thereby reducing the moment of inertia of the servo motor rotor.
Post a Comment:
You may also like:
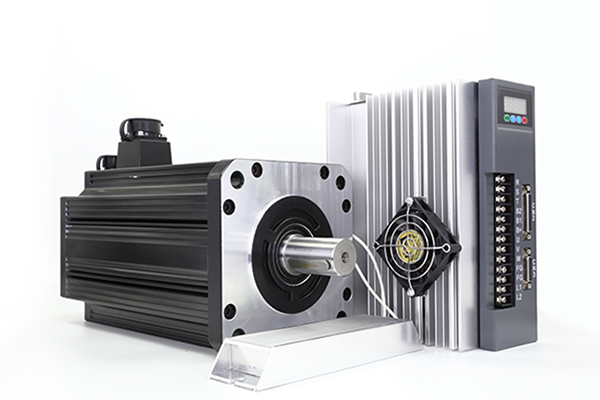
Category
Featured Articles
Difference Between Servo and Stepper ...
Servo motor and stepper motor are almost used in all automated industries where high precision is to be achieved. Though servo ...
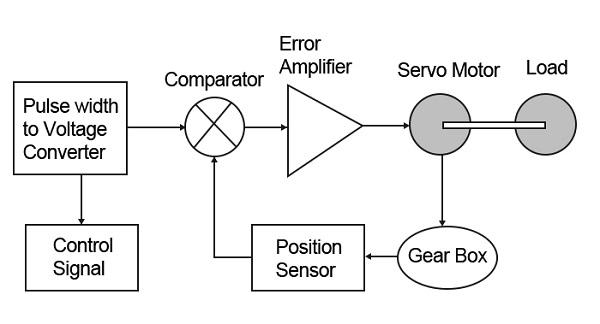
Why Use Servo Motor as Test Load?
Dynamometer is mainly divided into two parts: cabinet and frame, while the frame mainly has the motor under test, torque speed ...
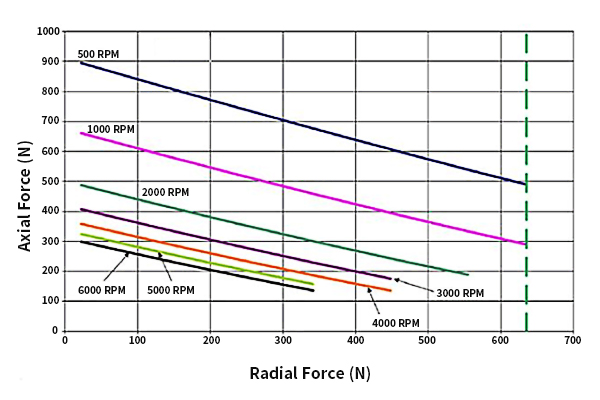
Safety Precaution For Using Servo Motor
In the realm of industrial automation, servo motors play a crucial role in achieving precision and control. These devices are ...
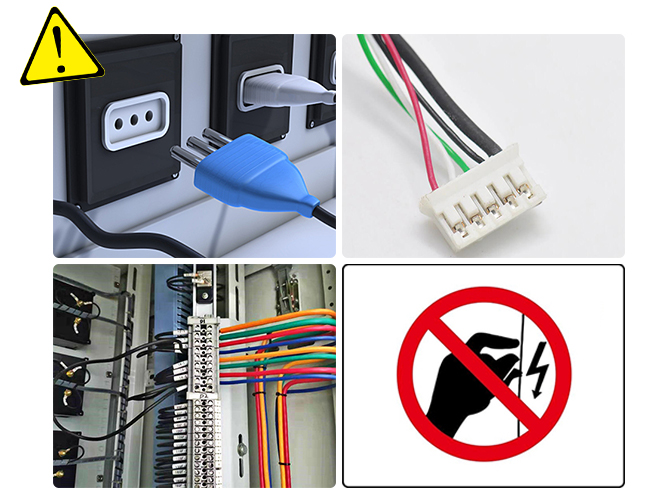
Troubleshooting of Servo Motor
Servo motors play a crucial role in various industrial applications, providing precision control and efficient performance. ...
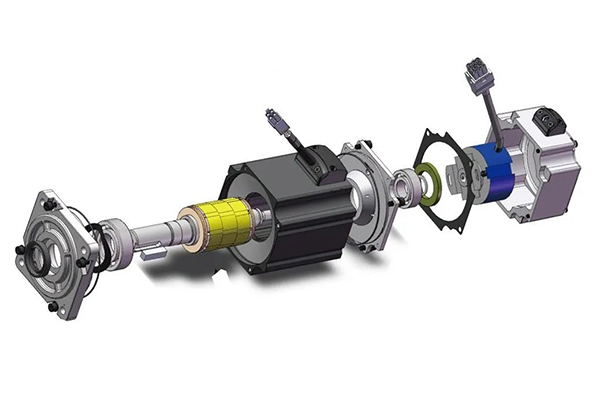