Difference Between Servo and Stepper Motors
Servo motor and stepper motor are almost used in all automated industries where high precision is to be achieved. Though servo and stepper motor can provide adequate torque with high accuracy, it is prominently important to choose the best one based on the performance ratio of these two motors. The decision for picking out the most appropriate of the two alternatives has many criteria. Hence the technical parameters such as speed, Torque, acceleration and competitive price are focused in this article.
Introduction
Servomotor is used as an electric actuator to convert electrical signal in to angular displacement or angular velocity on the shaft of the motor. Servo motor consists of two windings. One is permanent magnet rotor and another one is a stator winding. Unlike other motors it rotates from 0 to 180 degree only. In order to generate PWM pulses in terms of duty cycles, microcontroller is used. Hence more accurate control is quietly possible.
In servo motor potentiometer is used as position feedback sensor. The feedback signal corresponding to the present position of the load which is connected with servo motor shaft is obtained by using a position sensor. The potentiometer produces the voltage corresponding to the position angle of the motor shaft through gear mechanism. Then the feedback position sensor signal interms of voltage is applied at the input of error detector. It compares the voltage related to present position of the motor shaft with respect to the set or desired voltage related to desired position of the shaft obtained by pulse width to voltage converter then it produces the error signal either a positive or negative voltage.
The error signal available at the output of error detector is not enough to drive the servo motor. In order to amplify the error signal, error amplifier is used. Then the amplified voltage and power level of the error signal is given to servo motor and then the shaft of the motor turns to desired position. The error amplifier amplifies the error voltage and correspondingly powers the servo motor till error exists. The motor rotates until the error signal attains zero value. If the error is negative, the input voltage gets reversed and hence the motor shaft rotates in the opposite direction.
Stepper motors consist of a rotor with permanent magnet and a stator winding. When an input supply is given to stator winding through pulse width to voltage converter, current flows through the particular stator winding which is energized and it sets up the magnetic field and magnetic poles are created in the stator winding and it generates a magnetic flux distribution. When the stator pole NS and the rotor pole SR align, they attract each other. Now the angular position of the stepper motor shaft gets changed. Suppose if same poles from stator and rotor such as NS and NR or SS and SR align they get repelled each other. Stepper motor has more number of pole counts typically in the order of 50 or more. Each pole of the stepper motor is energized by the drive unit. Stepper motor drive unit consists of control unit, pulse generator unit power drive unit and protection unit. The power drive unit amplifies the pulse generated by the pulse generation control unit and is directly coupled with the stepping motor which belongs to the power interface between the stepping motor and micro controller. The stepping motor which belongs to the power interface between the stepping motor and micro controller.
Stepper motor has appreciable salient feature. As stepper motors don’t require closed loop as they are easily run in open-loop system. Hence it eliminates the design cost and complexity of an encoder or resolver circuit. Due to high pole count of stepper motor a very high torque at zero speed is quietly possible. They are compact and most economical.
Toque Speed Characteristic of Servo and Stepper Motor
Torque versus speed curves in which the green curve shows that the stepper motor produces high torque even at zero speed and torque falls as speed increases. In contrast, servo-motor torque remains constant over the entire operating range which is clearly indicated by blue and red curves. As servo motor incorporates feedback encoder, it enables the system to achieve accuracy as well as resolution through which the stability of the servo motor becomes quite stable. Hence desired position is easily achieved. Due to this salient feature servo motors can deliver torques up to 250 foot-pounds. Stepper motor can be quite competitive. But stepper motor resembles the mass-spring nature it may result in a few lost of steps. The steps which lost are not carried over from rotation to rotation. Stepper motors typically don’t require feedback closed loop system. More over stepper motors use less expensive magnets and rarely incorporate speed reduction gearbox. Stepper motor is less expensive comparing with servo motor.
Advantages And Limitation Of Servo and Stepper Motor
The applications where the parameters such as low speed low acceleration, and low accuracy require, there stepper motor is preferred. Also it tends to be compact and inexpensive. This makes these motors a good fit for automated manufacturing industries, medical, biotech, security surveillance, defense and semiconductor manufacturing applications. Servo motors offer an undeniable performance in terms of repeatability. Servo motors are a best choice for systems requiring high accuracy, high acceleration, and high speed. But the design of servo motor has more complexity and more cost. Servo motors are typically used in automatic packing industries, solar maximum power point tracking system, missile tracking and similar applications. If the motor performance is the most important aspect, a servo motor is the suitable choice. But we need to pay more. Amidst all those advantages, stepper motors have a few limitations which can cause significant implementation and operation issues depending on the applications. Stepper motors don’t suffer with any reverse power. In fact, stepper motors lose a significant amount of their torque when they approach maximum speed. Stepper motors are also not as good as servo motors in accelerating a load. When stepper motor is loaded with high speed it fails to generate sufficient torque to move to the next step before it receiving the next pulse which results a loss in position. If positional accuracy is considered essential criteria, the load on the motor should never be exceeded its maximum torque or else the stepper motor should be incorporated with a position encoder to ensure positional accuracy. In certain speed condition stepper motors also suffer from vibration and resonance problems depending on the load dynamics. Servo motors have the ability in delivering more torque than stepper motors but servo motor circuit design is more complex and it requires additional feedback position sensor. Servo motors often require speed reduction gear boxes to achieve low speed operation. More over the accessories like encoder required for servo motor increases the design complexity, cost and it requires frequent maintenance.
Conclusion
Stepper motor is preferred where quite slow, precise rotation, easy set up and controls are required. Stepper motor drive system is less expensive and is well suited for the applications that require low acceleration, high holding torque, and the flexibility of open or closed loop operation is not vitally important. Servo motor incorporated with closed loop control systems is best suitable to high speed, high torque applications that involve dynamic load changes. More over the choice of motor is also based on the Torque requirement, load mass and inertia, Speed requirement, desired acceleration and cost target.
Introduction
Servomotor is used as an electric actuator to convert electrical signal in to angular displacement or angular velocity on the shaft of the motor. Servo motor consists of two windings. One is permanent magnet rotor and another one is a stator winding. Unlike other motors it rotates from 0 to 180 degree only. In order to generate PWM pulses in terms of duty cycles, microcontroller is used. Hence more accurate control is quietly possible.
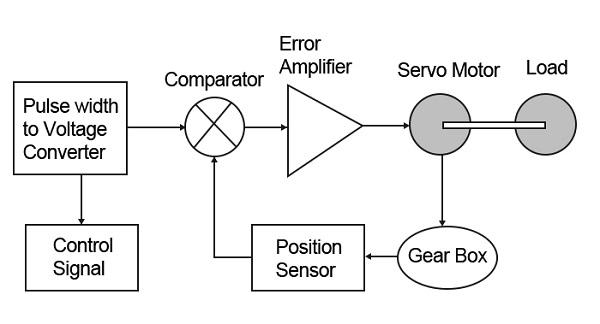
The error signal available at the output of error detector is not enough to drive the servo motor. In order to amplify the error signal, error amplifier is used. Then the amplified voltage and power level of the error signal is given to servo motor and then the shaft of the motor turns to desired position. The error amplifier amplifies the error voltage and correspondingly powers the servo motor till error exists. The motor rotates until the error signal attains zero value. If the error is negative, the input voltage gets reversed and hence the motor shaft rotates in the opposite direction.
Stepper motors consist of a rotor with permanent magnet and a stator winding. When an input supply is given to stator winding through pulse width to voltage converter, current flows through the particular stator winding which is energized and it sets up the magnetic field and magnetic poles are created in the stator winding and it generates a magnetic flux distribution. When the stator pole NS and the rotor pole SR align, they attract each other. Now the angular position of the stepper motor shaft gets changed. Suppose if same poles from stator and rotor such as NS and NR or SS and SR align they get repelled each other. Stepper motor has more number of pole counts typically in the order of 50 or more. Each pole of the stepper motor is energized by the drive unit. Stepper motor drive unit consists of control unit, pulse generator unit power drive unit and protection unit. The power drive unit amplifies the pulse generated by the pulse generation control unit and is directly coupled with the stepping motor which belongs to the power interface between the stepping motor and micro controller. The stepping motor which belongs to the power interface between the stepping motor and micro controller.
Stepper motor has appreciable salient feature. As stepper motors don’t require closed loop as they are easily run in open-loop system. Hence it eliminates the design cost and complexity of an encoder or resolver circuit. Due to high pole count of stepper motor a very high torque at zero speed is quietly possible. They are compact and most economical.
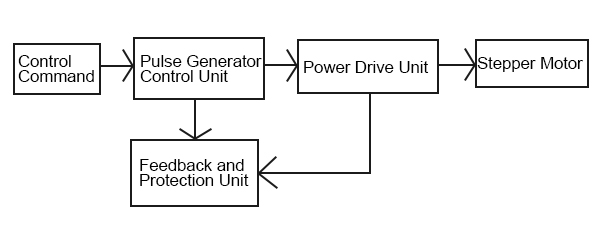
Torque versus speed curves in which the green curve shows that the stepper motor produces high torque even at zero speed and torque falls as speed increases. In contrast, servo-motor torque remains constant over the entire operating range which is clearly indicated by blue and red curves. As servo motor incorporates feedback encoder, it enables the system to achieve accuracy as well as resolution through which the stability of the servo motor becomes quite stable. Hence desired position is easily achieved. Due to this salient feature servo motors can deliver torques up to 250 foot-pounds. Stepper motor can be quite competitive. But stepper motor resembles the mass-spring nature it may result in a few lost of steps. The steps which lost are not carried over from rotation to rotation. Stepper motors typically don’t require feedback closed loop system. More over stepper motors use less expensive magnets and rarely incorporate speed reduction gearbox. Stepper motor is less expensive comparing with servo motor.
Advantages And Limitation Of Servo and Stepper Motor
The applications where the parameters such as low speed low acceleration, and low accuracy require, there stepper motor is preferred. Also it tends to be compact and inexpensive. This makes these motors a good fit for automated manufacturing industries, medical, biotech, security surveillance, defense and semiconductor manufacturing applications. Servo motors offer an undeniable performance in terms of repeatability. Servo motors are a best choice for systems requiring high accuracy, high acceleration, and high speed. But the design of servo motor has more complexity and more cost. Servo motors are typically used in automatic packing industries, solar maximum power point tracking system, missile tracking and similar applications. If the motor performance is the most important aspect, a servo motor is the suitable choice. But we need to pay more. Amidst all those advantages, stepper motors have a few limitations which can cause significant implementation and operation issues depending on the applications. Stepper motors don’t suffer with any reverse power. In fact, stepper motors lose a significant amount of their torque when they approach maximum speed. Stepper motors are also not as good as servo motors in accelerating a load. When stepper motor is loaded with high speed it fails to generate sufficient torque to move to the next step before it receiving the next pulse which results a loss in position. If positional accuracy is considered essential criteria, the load on the motor should never be exceeded its maximum torque or else the stepper motor should be incorporated with a position encoder to ensure positional accuracy. In certain speed condition stepper motors also suffer from vibration and resonance problems depending on the load dynamics. Servo motors have the ability in delivering more torque than stepper motors but servo motor circuit design is more complex and it requires additional feedback position sensor. Servo motors often require speed reduction gear boxes to achieve low speed operation. More over the accessories like encoder required for servo motor increases the design complexity, cost and it requires frequent maintenance.
Conclusion
Stepper motor is preferred where quite slow, precise rotation, easy set up and controls are required. Stepper motor drive system is less expensive and is well suited for the applications that require low acceleration, high holding torque, and the flexibility of open or closed loop operation is not vitally important. Servo motor incorporated with closed loop control systems is best suitable to high speed, high torque applications that involve dynamic load changes. More over the choice of motor is also based on the Torque requirement, load mass and inertia, Speed requirement, desired acceleration and cost target.
Post a Comment:
You may also like:
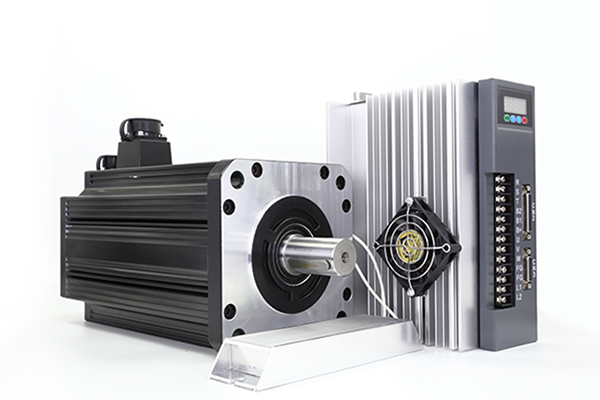
Category
Featured Articles
Troubleshooting of Servo Motor
Servo motors play a crucial role in various industrial applications, providing precision control and efficient performance. ...
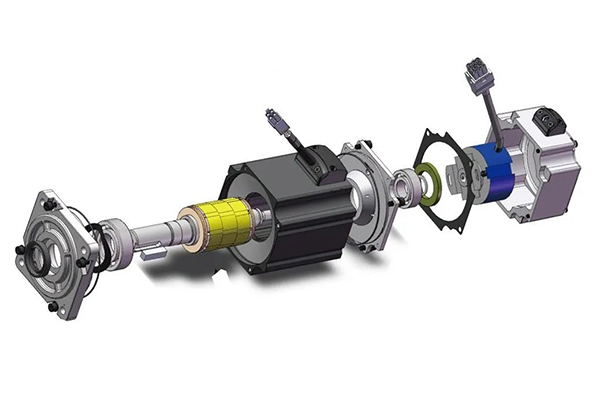
Safety Precaution For Using Servo Motor
In the realm of industrial automation, servo motors play a crucial role in achieving precision and control. These devices are ...
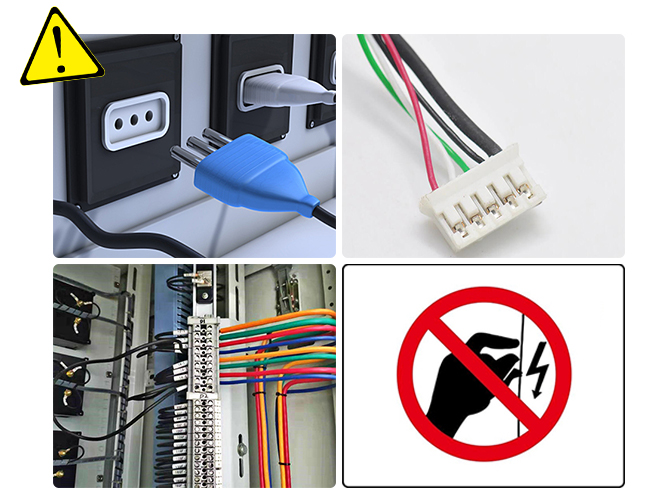
Why Use Servo Motor as Test Load?
Dynamometer is mainly divided into two parts: cabinet and frame, while the frame mainly has the motor under test, torque speed ...
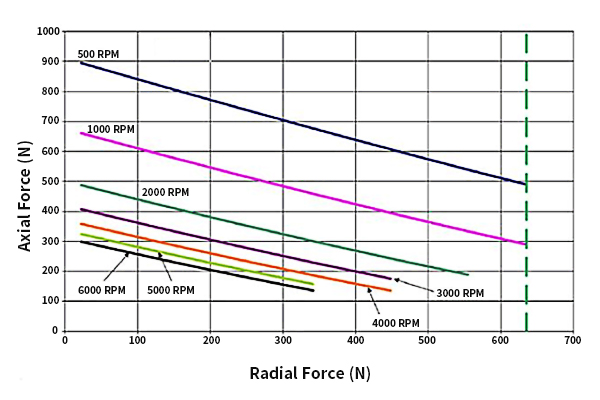
Difference Between Servo and Stepper ...
Servo motor and stepper motor are almost used in all automated industries where high precision is to be achieved. Though servo ...
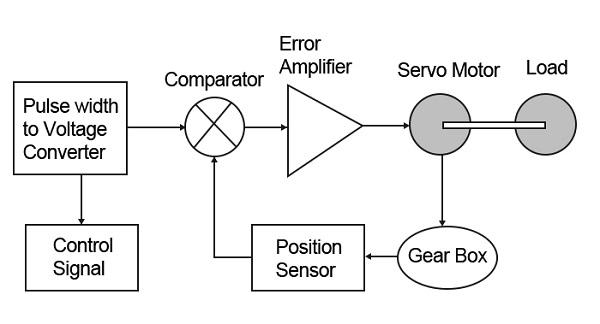