Servo Motors vs VFD
Servo motors and VFDs are typically comprised of two parts - the motor itself and a controller (also called "amplifier", "servo pack" or "inverter") which drives the motor and is connected to it by cable. The controller receives power from AC mains: a single phase for low-to-medium power drives and three phases for high-power drives. A typical manufacturing and robotic tool may have as little as one and as many as 20 such drives. Servo motors have a feedback circuit that allows them to maintain specific positions with high accuracy. This also means that servo motors work even when they are not moving. Variable frequency drives (VFD) work differently - their speed is controlled by the frequency of the
drive signal. What is common between these two different types of drives is that both are driven by pulsed signals.
Servo motors and VFD are driven by three-phase pulses with the repetition frequency ranging typically between 60kHz and 20kHz. Pulse has sharp edges only a few nanoseconds long. While the drive pulse frequency by itself seldom causes problems, the sharp edges of the pulses do. Sharp edges have a very wide spectrum extending into the Megahertz range. Capacitive coupling prevalent in motors and cables presents very low impedance for such signals. The result is significant high-frequency voltage on the rotor and subsequent ground currents through bearings. The particular current shown is 20mA question may be asked how can such a seemingly low current do any damage? If this current was a one-time occurrence it wouldn't cause concern. But these current spikes occur up to 40000 times per second every second - the servo motor works even when it is not moving. Such continuous hammering and chiseling can and does cause deterioration of bearings just like a small stream carves in time a deep path in stone.
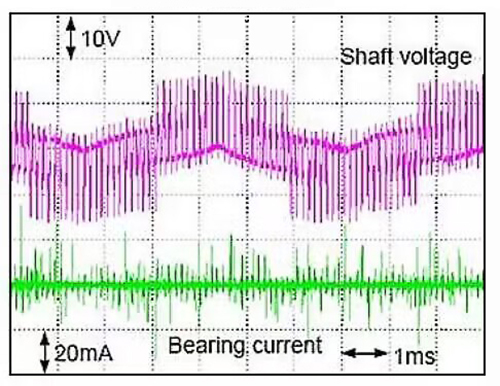
High-Frequency Noise in Equipment
Sharp pulse edges and resulting ground servo current not only cause problems for the bearings, but they also pollute the entire machine, especially its ground, by strong sharp transients with the repetition rate of that of drive pulses. The resulting signals can be high enough to cause interference with the equipment's electronics and electrical overstress (EOS) to sensitive components. AC power line ground current spikes occur every time there is a drive pulse edge. With the sensitivity of the current probe of 5mA/mV (CT1 probe), this voltage translates to ~ 1.8A of high-frequency noise current in the power line ground.
Interference with Operation of Equipment
High-frequency electrical noise (often called EMI – electromagnetic interference) raises the overall noise level in equipment. This causes random undesirable equipment behavior, data errors, and outright equipment lockups. It is not uncommon to find noise levels in equipment of the same magnitude or higher than the legitimate data signals. This affects the normal operation of computerized equipment and alters sensor readings. Once noise gets into the equipment' circuits, it is very difficult to remove it - a much better option is not to let servo motor operation pollute the equipment.
Electrical Overstress
Equipment handling sensitive components, such as pick-and-place tools in electronic assembly, IC handlers and wire bonders in semiconductor manufacturing, and other similar tools handle components that can be damaged by levels as low as a fraction of a volt for electronic assembly. This current is synchronized with the drive pulses of the servo motor (servo current pulses that appear out of sync with the pulses are well-synchronized with the operation of other drives in the IC handler).
Mitigation of High-Frequency Noise in Servo Motors and VFD
Mechanical solutions such as ceramic bearings and bearing protection brush rings do not reduce overall EMI levels in equipment while requiring different physical sizes to fit a particular motor model, and being subject to wear, performance deterioration, inspection, and maintenance with its associated ongoing cost. Special reactors which are simply inductors connected in line with each phase of the drive signal offer marginal improvements plus they are often bulky and require special installation, both electrical and mechanical.
Servo motors and VFD are driven by three-phase pulses with the repetition frequency ranging typically between 60kHz and 20kHz. Pulse has sharp edges only a few nanoseconds long. While the drive pulse frequency by itself seldom causes problems, the sharp edges of the pulses do. Sharp edges have a very wide spectrum extending into the Megahertz range. Capacitive coupling prevalent in motors and cables presents very low impedance for such signals. The result is significant high-frequency voltage on the rotor and subsequent ground currents through bearings. The particular current shown is 20mA question may be asked how can such a seemingly low current do any damage? If this current was a one-time occurrence it wouldn't cause concern. But these current spikes occur up to 40000 times per second every second - the servo motor works even when it is not moving. Such continuous hammering and chiseling can and does cause deterioration of bearings just like a small stream carves in time a deep path in stone.
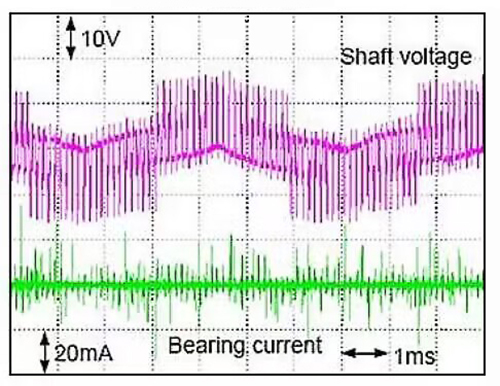
High-Frequency Noise in Equipment
Sharp pulse edges and resulting ground servo current not only cause problems for the bearings, but they also pollute the entire machine, especially its ground, by strong sharp transients with the repetition rate of that of drive pulses. The resulting signals can be high enough to cause interference with the equipment's electronics and electrical overstress (EOS) to sensitive components. AC power line ground current spikes occur every time there is a drive pulse edge. With the sensitivity of the current probe of 5mA/mV (CT1 probe), this voltage translates to ~ 1.8A of high-frequency noise current in the power line ground.
Interference with Operation of Equipment
High-frequency electrical noise (often called EMI – electromagnetic interference) raises the overall noise level in equipment. This causes random undesirable equipment behavior, data errors, and outright equipment lockups. It is not uncommon to find noise levels in equipment of the same magnitude or higher than the legitimate data signals. This affects the normal operation of computerized equipment and alters sensor readings. Once noise gets into the equipment' circuits, it is very difficult to remove it - a much better option is not to let servo motor operation pollute the equipment.
Electrical Overstress
Equipment handling sensitive components, such as pick-and-place tools in electronic assembly, IC handlers and wire bonders in semiconductor manufacturing, and other similar tools handle components that can be damaged by levels as low as a fraction of a volt for electronic assembly. This current is synchronized with the drive pulses of the servo motor (servo current pulses that appear out of sync with the pulses are well-synchronized with the operation of other drives in the IC handler).
Mitigation of High-Frequency Noise in Servo Motors and VFD
Mechanical solutions such as ceramic bearings and bearing protection brush rings do not reduce overall EMI levels in equipment while requiring different physical sizes to fit a particular motor model, and being subject to wear, performance deterioration, inspection, and maintenance with its associated ongoing cost. Special reactors which are simply inductors connected in line with each phase of the drive signal offer marginal improvements plus they are often bulky and require special installation, both electrical and mechanical.
Post a Comment:
You may also like:
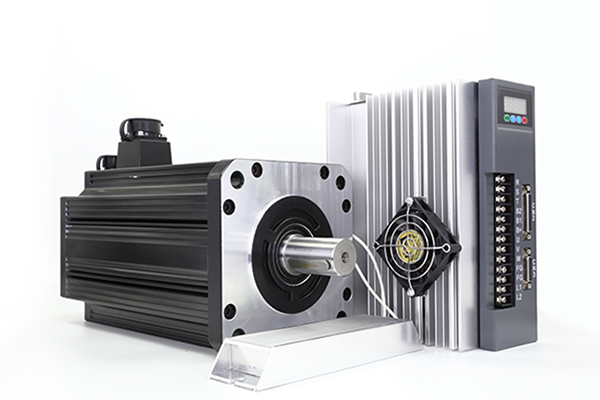
Category
Featured Articles
Troubleshooting of Servo Motor
Servo motors play a crucial role in various industrial applications, providing precision control and efficient performance. ...
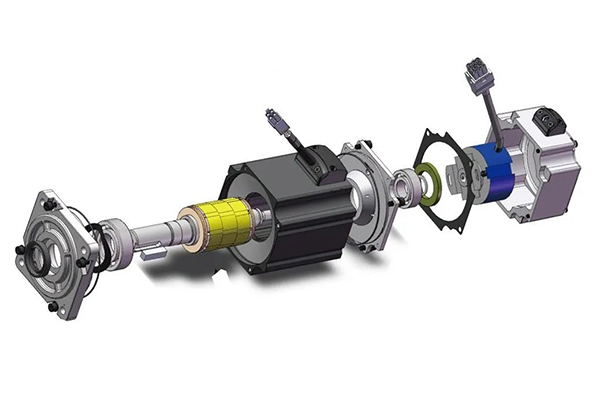
Safety Precaution For Using Servo Motor
In the realm of industrial automation, servo motors play a crucial role in achieving precision and control. These devices are ...
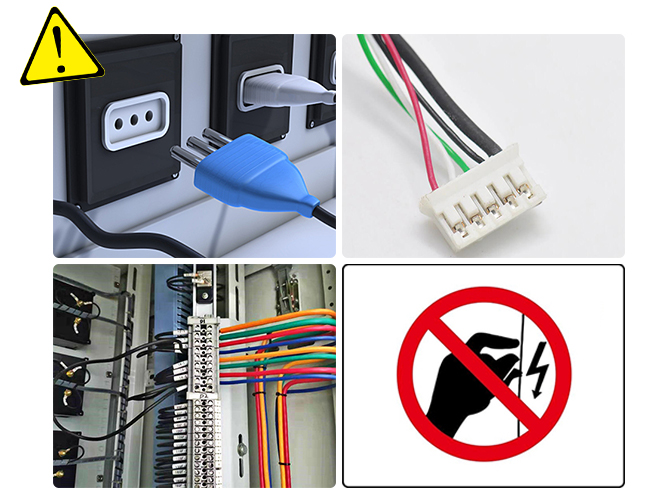
Why Use Servo Motor as Test Load?
Dynamometer is mainly divided into two parts: cabinet and frame, while the frame mainly has the motor under test, torque speed ...
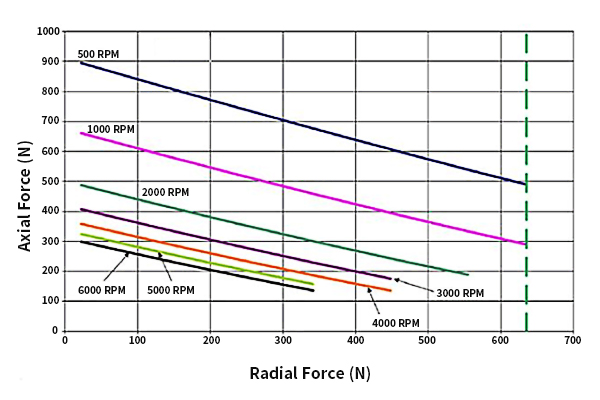
Difference Between Servo and Stepper ...
Servo motor and stepper motor are almost used in all automated industries where high precision is to be achieved. Though servo ...
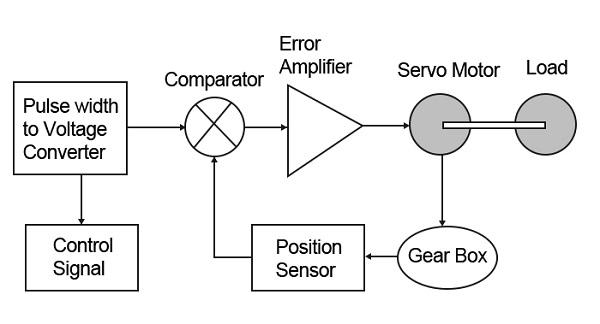