Home » Servo System » Hobby Servo vs. Industrial Servo Systems
Hobby Servo vs. Industrial Servo Systems
Both hobbyists and industrial companies use "servos", but they are quite different in their components and applications. We use both extensively, depending on the best fit for the project. Here is a short discussion of the differences between them in several key areas.
Control Loops
Industrial servo system is usually made up of a traditional PID loop, where sensor(s) measure velocity and position of the motor or moving mass, and adjust torque (current) to keep errors small. An example is a motor with an encoder connected to a ballscrew. The precision and accuracy, can be quite high, commonly and easily measured in less than a thousandth of an inch or revolution. The current control is done by Pulse Width Modulation (PWM) at frequencies of 20 kHz or more, out of the audible range.
Hobby control loops got designed around the human as the main sensor. In essence, the human gives a speed command with a joystick, and the servo gets a boost of current to try to accelerate. The PWM current control uses less expensive transistors, so it is common for there to be an annoying whine around 7 kHz. If a position sensor is added to a motor to control position, for instance in a camera gimble or a steering mechanism, it is relatively low resolution, and to maintain that position, it hunts back and forth between counts. Sometimes this hunting is noticable if applied to more precise devices, but most of the time other slop in the system makes it a non-issue. As you progress toward autonomous operation, as in drones, then other sensors are added to replace the human, such as barometers for elevation, sonar for distance detection, 3-d accelerometers (like in your smartphone), GPS for gross positioning, and a compass. These fomulaically combine, sometimes even using a rough PID algorithm, and replace the external joystick command with an internal joystick-equivalent.
Life Expectancy
This may be the biggest factor in the cost of an industrial system compared to hobby. These components need to last the life of the usefulness of the machine, which generally is justified over at least a lifespan of that machine's product.
Brushless hobby motor manufacturers suggest changing motor bearings after 60 hours of use. There are some worse and some better, but still the point is the units are hours, not years. Additionally, because of the rough use of the vehicles, the whole vehicle may not last that long before it is pretty much needs a complete rebuild.
Power Source
Industrial: most machines will have access to a line voltage that has a big power plant at the other end of the wire. In any motor, the parameter that limits its performance is its ability to dissipate heat. Heat in a motor, in Watts, is P=I*I*R, so keeping current low is important. To get power with low current, you need higher voltages. It is common for the bus voltage of an amplifier to run at line voltage rectified, which for 115 VAC means 163 Vdc, and a 230 VAC system would have a 320 Vdc bus voltage. This means that the power transistors providing the current need to switch voltages in those ranges, not in the TTL (5V) range. This is the primary contributor toward the relatively high cost of industrial amplifiers compared to hobby ESC's.
Hobby vehicles move mass in a very unorganized fashion, and need to carry their own energy source on board. Mostly this means a battery pack of some sort, and this (along with other consumer electronics) has driven a large change in battery technology. The latest batteries that have a relatively high energy density is the Lithium Polymer battery, a cousin of the much safer Lithium-Ion battery found in nearly every portable device we power with rechargeable batteries. Li-Po's are a fire hazard. We charge them in a special fire-resistant battery bag OUTSIDE. And we use them to get just a little more play time from the hobby. Battery voltage is still in the 7 to 22 Vdc range, nowhere close to industrial voltages. So motors just cannot be near as efficient in comparison. When specifying a motor, one of the key specs will be how hot that motor will get during use. But the hobby has one key difference - duty cycle. The motor may get hot, but the battery then needs a recharge, so there is plenty of cool-down time. To get around the limited play time of carrying energy in a battery, one can switch to a liquid fuel and a small engine to burn it. An ounce of fuel has many times the energy density of our best batteries. This concept is the driving reason that our high-mass transportation system runs on liquid fuels, not batteries - energy density. A single power plant works fine for the main drive axis in single-shaft hobby applications like a fixed wing aircraft or a ripping 4x4 scale model. But try making a single shaft work in a multi-rotor copter, where three to eight motors/props adjust to different speeds to maintain orientation.
Control Loops
Industrial servo system is usually made up of a traditional PID loop, where sensor(s) measure velocity and position of the motor or moving mass, and adjust torque (current) to keep errors small. An example is a motor with an encoder connected to a ballscrew. The precision and accuracy, can be quite high, commonly and easily measured in less than a thousandth of an inch or revolution. The current control is done by Pulse Width Modulation (PWM) at frequencies of 20 kHz or more, out of the audible range.
Hobby control loops got designed around the human as the main sensor. In essence, the human gives a speed command with a joystick, and the servo gets a boost of current to try to accelerate. The PWM current control uses less expensive transistors, so it is common for there to be an annoying whine around 7 kHz. If a position sensor is added to a motor to control position, for instance in a camera gimble or a steering mechanism, it is relatively low resolution, and to maintain that position, it hunts back and forth between counts. Sometimes this hunting is noticable if applied to more precise devices, but most of the time other slop in the system makes it a non-issue. As you progress toward autonomous operation, as in drones, then other sensors are added to replace the human, such as barometers for elevation, sonar for distance detection, 3-d accelerometers (like in your smartphone), GPS for gross positioning, and a compass. These fomulaically combine, sometimes even using a rough PID algorithm, and replace the external joystick command with an internal joystick-equivalent.
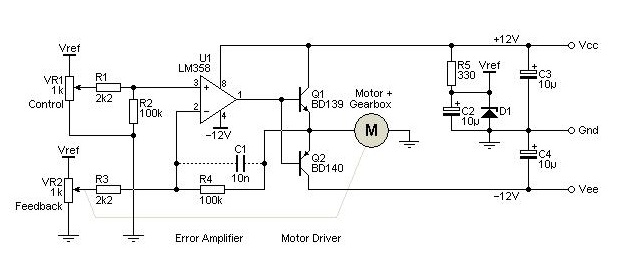
This may be the biggest factor in the cost of an industrial system compared to hobby. These components need to last the life of the usefulness of the machine, which generally is justified over at least a lifespan of that machine's product.
Brushless hobby motor manufacturers suggest changing motor bearings after 60 hours of use. There are some worse and some better, but still the point is the units are hours, not years. Additionally, because of the rough use of the vehicles, the whole vehicle may not last that long before it is pretty much needs a complete rebuild.
Power Source
Industrial: most machines will have access to a line voltage that has a big power plant at the other end of the wire. In any motor, the parameter that limits its performance is its ability to dissipate heat. Heat in a motor, in Watts, is P=I*I*R, so keeping current low is important. To get power with low current, you need higher voltages. It is common for the bus voltage of an amplifier to run at line voltage rectified, which for 115 VAC means 163 Vdc, and a 230 VAC system would have a 320 Vdc bus voltage. This means that the power transistors providing the current need to switch voltages in those ranges, not in the TTL (5V) range. This is the primary contributor toward the relatively high cost of industrial amplifiers compared to hobby ESC's.
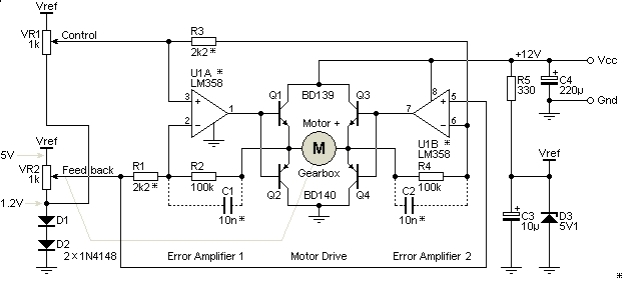
Post a Comment:
You may also like:
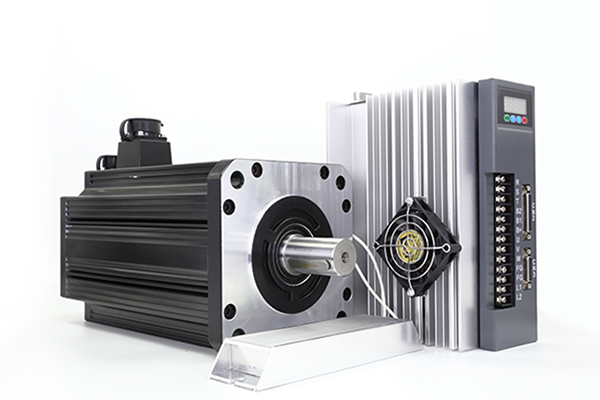
Category
Featured Articles
What are the Basic Components of ...
Servomechanisms, called servos for short, are the basic building blocks of power drives. In this manual what we mean by a power ...
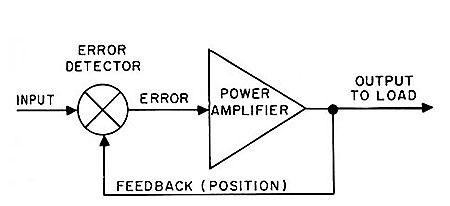
What is the Bandwidth of ...
For a servo system, the bandwidth is the maximum sine wave frequency to which the servo system can respond. In professional ...
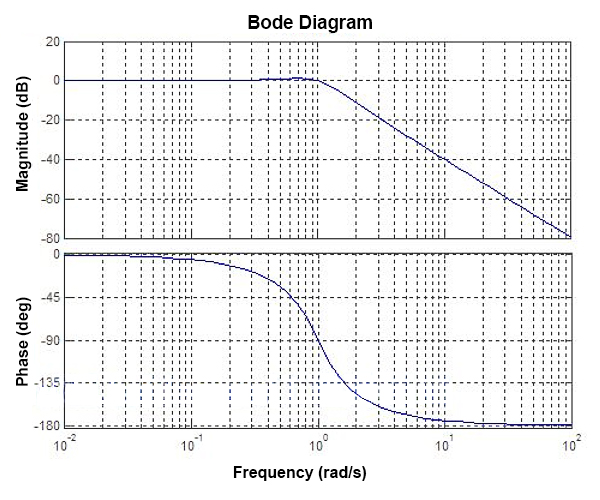
What Should Consider Before Using ...
Servo system is a commonly used control system, widely used in industrial automation. It compares the output signal with the ...
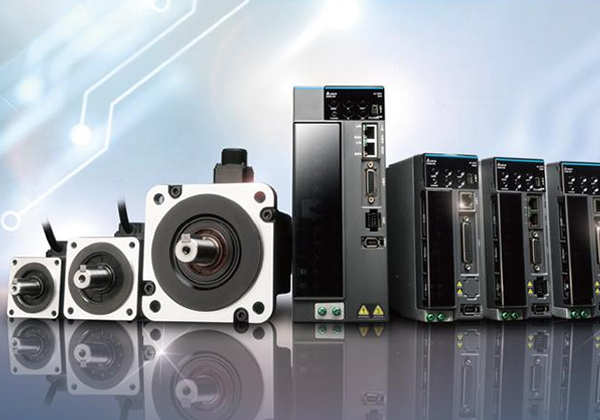
What is Servo System?
A feedback control system used to precisely follow or reproduce a process. Also known as a follower system. In many cases, a ...
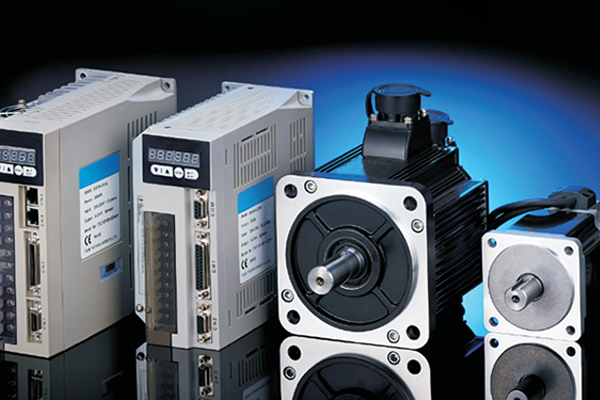