Home » Servo Drive » Servo Motor Driver
Servo Motor Driver
ATO suppliers provide servo drives. Servo drive, also known as a servo controller, is a controller used to control servo motors. Three-phase 220V AC servo drivers are mainly used in high-voltage applications and precise positioning systems, it is widely used in industrial robots, CNC machining centers, and other automation equipment. The servo driver with innovation design can perform short-distance rapid positioning operations and is easy to operate.
Specification
Details
An AC servo drive and an AC servo motor work in tandem to achieve precise control and efficient motion in various applications. The link between them is critical for the seamless functioning of a servo system. At the core of this link is the closed-loop control system, which comprises the servo drive and motor. The servo drive serves as the brain of the system, receiving commands and feedback signals. It converts the incoming electrical signals into the appropriate power output needed for the motor. This power is then transmitted to the AC servo motor.
The AC servo motor is responsible for translating electrical energy into mechanical motion. It consists of a rotor and a stator, where the stator is energized by the output from the servo drive. The interaction between the magnetic fields of the rotor and stator generates motion. The motor's rotor position and speed are constantly monitored by sensors, providing feedback to the servo drive.
The communication between the AC servo drive and motor is typically facilitated through a feedback loop. Encoders or resolvers on the motor provide position and speed information, allowing the drive to adjust the power supplied to the motor in real-time. This feedback mechanism enables the system to correct errors and discrepancies, ensuring accurate and precise control of the motor.
The link between the AC servo drive and motor is established through power and communication cables. These cables transmit the control signals from the drive to the motor and convey feedback information from the motor to the drive. Additionally, modern systems often utilize digital communication protocols like Pulse Width Modulation (PWM) or Serial Communication Interface (SCI) to enhance the speed and accuracy of data exchange between the drive and motor.
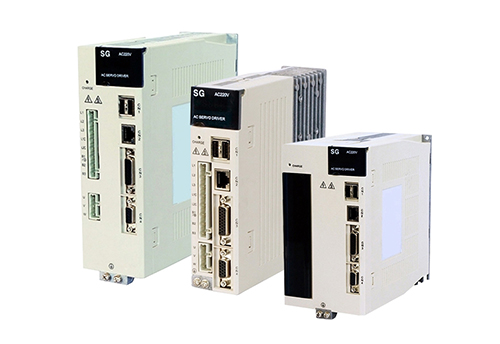
Model |
ATO-SG-AS |
Matching Servo Motor Model |
50W servo motor |
400W servo motor |
|
750W servo motor |
|
1.5kW servo motor |
|
2kW servo motor |
|
5.5kW servo motor |
|
Structure |
Base-mounted type |
Operate |
0°C~+ 50°C |
Humidity |
<90% (no frost) |
Encoder Feedback |
2500 lines incremental encoder |
17/23 bit absolute encoder |
|
Voltage |
Three phase 220V AC |
Input Signal Type |
Pulse + analog (±10V) signal or pulse signal (Optional) |
Control Mode |
Position control, Speed control, Jog operation |
Details
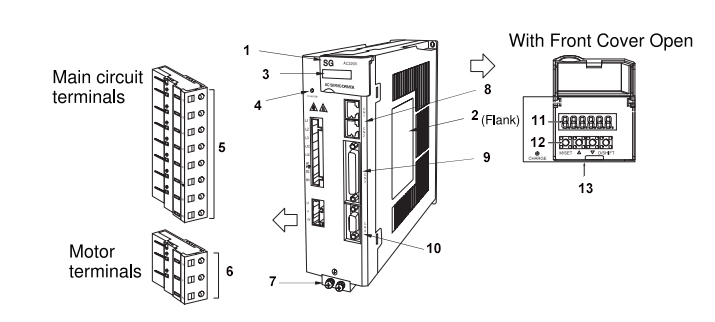
|
Name |
Description |
1 |
Front Cover |
/ |
2 |
Nameplate |
Indicates the SERVOPACK model and rating. |
3 |
Input Voltage |
/ |
4 |
Charge |
Lights up when the main circuit power is turned on. Note: Even if you turn OFF the main circuit power supply, this indicator will be lighting as long as the internal capacitor remains charged. Do not touch the main circuit or motor terminals while this indicator is lighting. Doing so may result in electric shocks. |
5 |
Main Circuit Terminals |
The terminals depend on the main circuit power supply input specifications of the SERVOPACK. |
6 |
Servo Motor Terminals (U,V,W) |
The connection terminals for the servo motor main circuit cable (power line). |
7 |
Ground Terminal |
The ground terminals to prevent electric shock. Always connect this terminal. |
8 |
485 Communication Connector (CN1,CN2) |
/ |
9 |
I/O Signal Connector (CN3) |
Connect to reference input signals and sequence I/O signals. |
10 |
Encoder Connector (CN4) |
Rotary servo motor: Connect to the encoder in the servo motor. Linear servo motor: Connect to a serial converter unit or linear encoder. |
11 |
Panel Display |
Used to display SERVOPACK status, alarm numbers, and parameters. |
12 |
Panel Operation keys |
Used to set parameters. |
13 |
Panel Operator |
/ |
An AC servo drive and an AC servo motor work in tandem to achieve precise control and efficient motion in various applications. The link between them is critical for the seamless functioning of a servo system. At the core of this link is the closed-loop control system, which comprises the servo drive and motor. The servo drive serves as the brain of the system, receiving commands and feedback signals. It converts the incoming electrical signals into the appropriate power output needed for the motor. This power is then transmitted to the AC servo motor.
The AC servo motor is responsible for translating electrical energy into mechanical motion. It consists of a rotor and a stator, where the stator is energized by the output from the servo drive. The interaction between the magnetic fields of the rotor and stator generates motion. The motor's rotor position and speed are constantly monitored by sensors, providing feedback to the servo drive.
The communication between the AC servo drive and motor is typically facilitated through a feedback loop. Encoders or resolvers on the motor provide position and speed information, allowing the drive to adjust the power supplied to the motor in real-time. This feedback mechanism enables the system to correct errors and discrepancies, ensuring accurate and precise control of the motor.
The link between the AC servo drive and motor is established through power and communication cables. These cables transmit the control signals from the drive to the motor and convey feedback information from the motor to the drive. Additionally, modern systems often utilize digital communication protocols like Pulse Width Modulation (PWM) or Serial Communication Interface (SCI) to enhance the speed and accuracy of data exchange between the drive and motor.
Post a Comment:
You may also like:
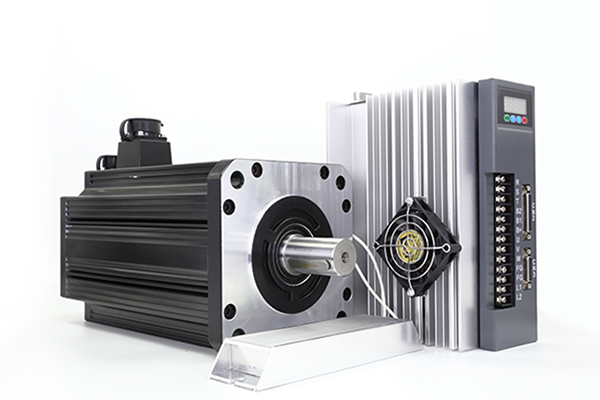
Category
Featured Articles
What are the Basics of Servo Drive?
Servo motors come in so many types and flavors that it is difficult to define them in a way that is accurate and universally ...
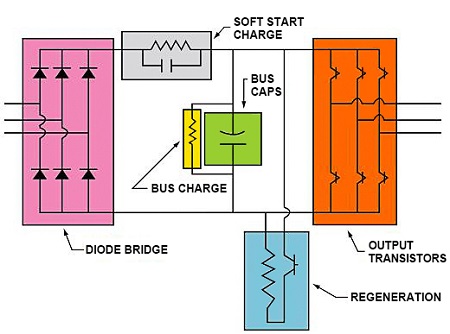
How to Install a Servo Drive?
Installing a servo drive involves several steps, and the specific process may vary depending on the manufacturer and model of the ...
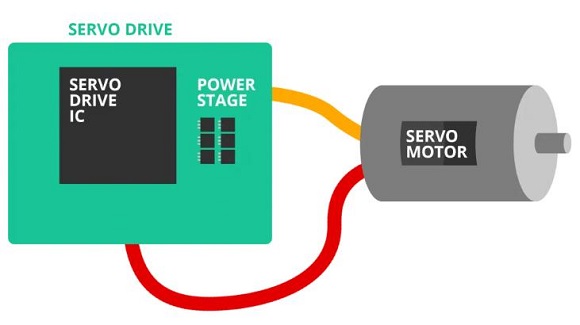
What are the Soft Start Techniques for ...
Servos (as commonly used in radio-controlled vehicles and small-scale robotics)are DC actuators that use a potentiometer to ...
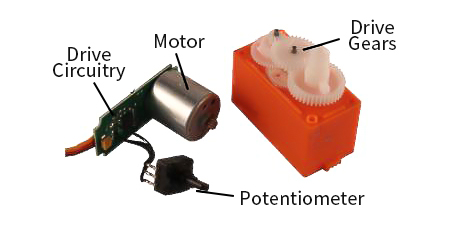
Servo Drive System vs. Variable ...
A servo drive system, as opposed to a variable frequency drive (VFD) or AC motor drive , has the ability to position with ...
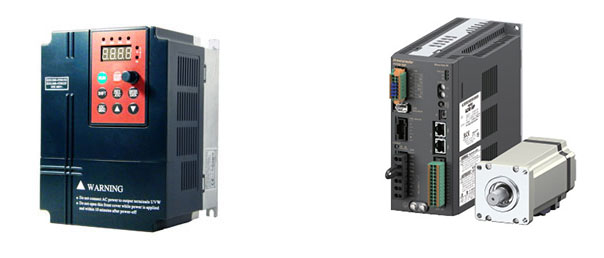