Home » DC Servo Motor » 500W 48V DC Servo Motor
500W 48V DC Servo Motor
ATO, as a professional manufacturer of servo motors, provides the right servo motor selection knowledge for customers in need. According to the actual needs to choose the right type of motor and specifications, such as motor size, output power,
voltage, current and so on. Next ATO introduces a high performance 500W DC servo motor.
Specifications
Mode:l No. ATO-110AS0405-15
Rated Power: 500W
Rated Voltage: 48 VDC
Rated current: 14 A
Rated torque: 3 Nm
Peak torque: 10.8 Nm
Rated speed: 1500 rpm
No-load speed: 1700 rpm
Operating efficiency: 85
Flange size: 110 mm
Weight: 7 kg
The 500 watt brushless DC servo motor has a low rated speed of 1500 rpm and a rated holding torque of 3 Nm. Brushless DC servomotors with IP55 protection operate at 48 volts and are supplied with 2,500 PPR incremental encoders. The quality is guaranteed by CE and ISO approvals. Constructed with Class F insulation, optimized winding end structure minimizes copper and iron losses, small size, light weight, low temperature rise and high efficiency (85%). The DC brushless servo motor with stable motor performance adopts NdFe35 permanent magnet material with strong anti-magnetization ability. Low noise and vibration, high torque and fast dynamic response. Compact size, easy to carry and install.
PWM (Pulse Width Modulation) control of DC motors is a common method used to control the speed and direction of DC motors. The basic principle of PWM control is to control the average voltage of the electric servo motor by adjusting the duty cycle of the square wave, thus realizing the speed and direction control of the motor.
In PWM control, DSP and other microprocessors will generate a PWM signal, the duty cycle of the signal can be adjusted to control the average voltage of the motor. Specifically, when the duty cycle of the PWM signal is large, the average voltage of the motor draft, turn fast; when the duty cycle of the PWM signal is small, the average voltage of the motor is small.
When the duty cycle of the PWM signal is small, the average voltage of the motor is low and it turns slowly. By adjusting the duty cycle of the PWM signal, continuous speed regulation and precise control of the motor can be realized. In PWM control, it is also necessary to consider the polarity control of the motor. Generally speaking, by changing the phase or polarity of the PWM signal, the direction of rotation of the motor can be changed.
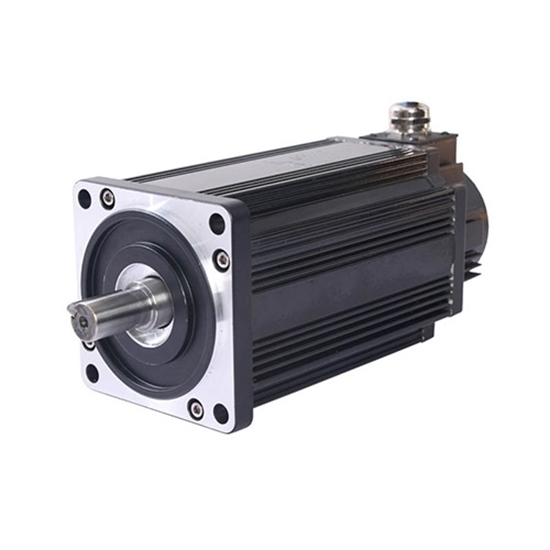
Specifications
Mode:l No. ATO-110AS0405-15
Rated Power: 500W
Rated Voltage: 48 VDC
Rated current: 14 A
Rated torque: 3 Nm
Peak torque: 10.8 Nm
Rated speed: 1500 rpm
No-load speed: 1700 rpm
Operating efficiency: 85
Flange size: 110 mm
Weight: 7 kg
The 500 watt brushless DC servo motor has a low rated speed of 1500 rpm and a rated holding torque of 3 Nm. Brushless DC servomotors with IP55 protection operate at 48 volts and are supplied with 2,500 PPR incremental encoders. The quality is guaranteed by CE and ISO approvals. Constructed with Class F insulation, optimized winding end structure minimizes copper and iron losses, small size, light weight, low temperature rise and high efficiency (85%). The DC brushless servo motor with stable motor performance adopts NdFe35 permanent magnet material with strong anti-magnetization ability. Low noise and vibration, high torque and fast dynamic response. Compact size, easy to carry and install.
PWM (Pulse Width Modulation) control of DC motors is a common method used to control the speed and direction of DC motors. The basic principle of PWM control is to control the average voltage of the electric servo motor by adjusting the duty cycle of the square wave, thus realizing the speed and direction control of the motor.
In PWM control, DSP and other microprocessors will generate a PWM signal, the duty cycle of the signal can be adjusted to control the average voltage of the motor. Specifically, when the duty cycle of the PWM signal is large, the average voltage of the motor draft, turn fast; when the duty cycle of the PWM signal is small, the average voltage of the motor is small.
When the duty cycle of the PWM signal is small, the average voltage of the motor is low and it turns slowly. By adjusting the duty cycle of the PWM signal, continuous speed regulation and precise control of the motor can be realized. In PWM control, it is also necessary to consider the polarity control of the motor. Generally speaking, by changing the phase or polarity of the PWM signal, the direction of rotation of the motor can be changed.
Post a Comment:
You may also like:
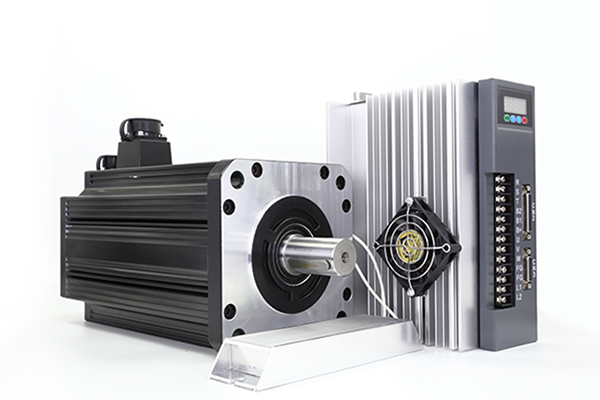
Category
Featured Articles
What is a Servo Motor?
There are some special types of application of electrical motor where rotation of the motor is required for just a certain angle ...
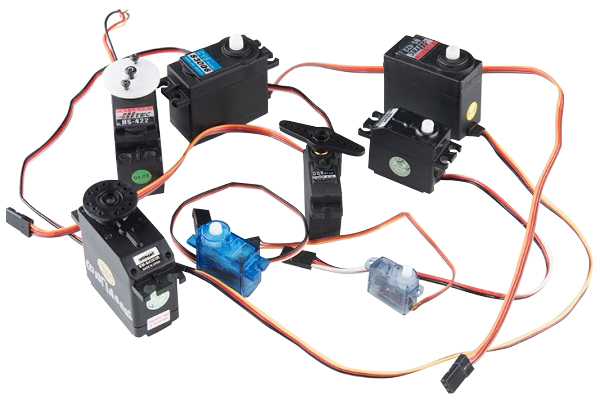
What are the Basics of Servo Drive?
Servo motors come in so many types and flavors that it is difficult to define them in a way that is accurate and universally ...
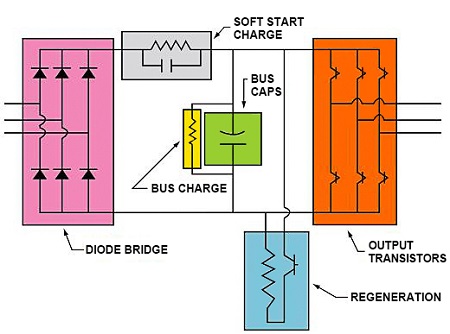
Why Use Servo Motor as Test Load?
Dynamometer is mainly divided into two parts: cabinet and frame, while the frame mainly has the motor under test, torque speed ...
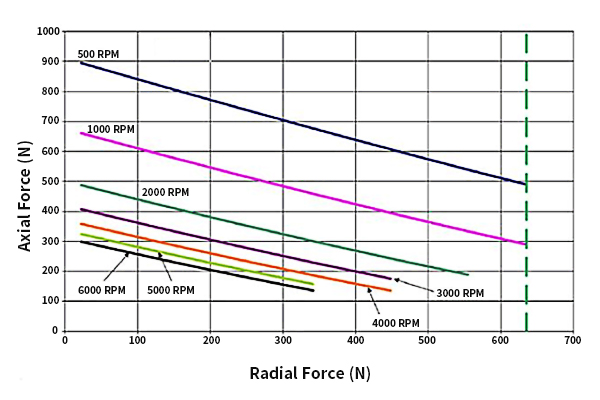
What Should Consider Before Using ...
Servo system is a commonly used control system, widely used in industrial automation. It compares the output signal with the ...
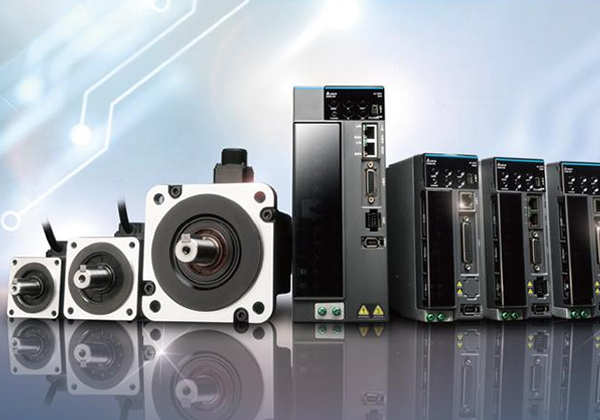
Servo Motor in Food Industry
In the ever-evolving landscape of the food industry, technological advancements play a pivotal role in enhancing efficiency, ...
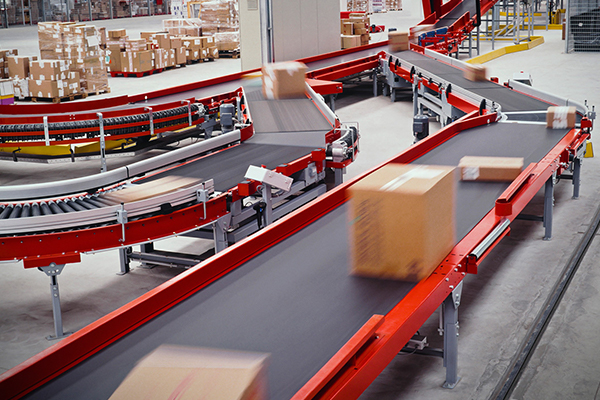