Which Servo Motor is Right for Machine Design?
Each technology has its niche, and since the selection of either of these technologies for a given application affects its chance of success, it is important for the machine designer to select the best motor-drive system for the application, while considering the technical advantages and disadvantages of both. It is all about utilizing these technologies with balance to achieve the desired process performance for a given machine design while balancing cost versus the capability of the required mechanism.
This article presents an overview of different baseline capabilities for selection criteria between stepper and servo technology. A thorough understanding of these technologies will help generate the best and most efficient mechatronic designs to bring forth the full capability of a machine. Today’s digital stepper motor drives provide enhanced drive features, option flexibility, and communication protocols using advanced integrated circuits and simplified programming techniques. The same is true of servo motor systems, while higher torque density, improved electronics, algorithms, and higher feedback resolution have resulted in higher system Bandwidth (BW) capabilities, and lower initial and overall operating costs for many applications.
Stepper Motor System Overview
Stepper motors have several major advantages over servo systems. They are typically lower cost, have common NEMA mountings, offer lower torque options, require less costly cabling, and their open loop motion control component makes machine integration simplistic and provides ease-of-use to end users.
Torque and Speed Considerations
The issue of whether to use a stepper or servo is dictated by the application in most cases. Steppers are typically sized for twice their continuous requirements for additional acceleration and/or deceleration torque capability or for a required peak torque. In contrast, servo motors are generally sized for the specific application velocities and torques for maximum intermittent acceleration/deceleration, holding torque (if applicable), and continuous RMS requirements over the complete motion profile.
In general, if an application requires high-throughput, high-speed, and high-bandwidth capability for disturbance correction, and/or high-rpm, with or without tight coordination between axes, servo motors are the best option. If point-to-point position performance and rpm requirements are modest, (as a function of the process loads and expected disturbances) steppers may be a better choice. Additionally, when the loads are within reason, a stepper’s ability to hold position (using holding torque with power and detent torque without power) can be an advantage.
Speed-torque curves highlight the difference between stepper and AC permanent magnet (PM) servo motors of equal volume. Steppers typically generate higher continuous torque at lower speeds than servo motors. However, servo motors produce intermittent peak torques in this same low-speed range and produce peak and continuous torques over a much wider-higher speed range.
Automated machine axes for adjustment and setup as well as video axes for inspection, are applications that stepper systems fulfill well. Steppers are especially ideal for these type axes because they tend to be easier to design into control systems and less expensive on initial setup. When an axis for a given setup can be locked into place they are less expensive to operate (e.g. optional ON/OFF reduced power mode). Additionally, when properly applied, steppers are less prone to failure because of their simplistic open-loop control, which only requires winding-to-drive match-up versus motor-drive-to-mechanism tuning required with feedback circuits of a closed-loop system.
Stepper Drives
Newer design techniques have improved step motor performance by the utilization of: built-in feedback,end-of-move damping (for reduced settling times while maximizing accuracy), soft-start (to reduce jerk on power-up), anti-resonance modes (for optimizing torque, stability, and noise reduction - audible or otherwise), Idle Current Reduction (IRC - for reduced motor heating during standstill) and easily controlled operation modes between full-step, half-step and micro stepping.
Although most properly sized steppers are extremely accurate running open loop in the selected step mode, built-in feedback provides additional precision without the cost of an external feedback device. Microstepping techniques result in smoother torque and motion at low speeds and greater resolution at high speeds with the reduction of step size from full-step/half-step.
Servo Motor System Overview
Servo motors have several distinct advantages over steppers. They can generate high torque over a wide speed range on demand, and are available in wider torque ranges and higher voltages (up to 480 Vac). They respond to disturbances with a torque much greater than their continuous capability and use only the power required to accomplish the commanded motion and are compact.
Servo Drives
Motor drive compensation often referred to as tuning or comp, once considered the bane process of servo users is, for the most part, history. Today, the newest digital servo drive technologies have enhanced software and hardware capabilities for improved user experience and offer remarkable compensation flexibility. In fact, some servo systems automatically configure the motor, drive and feedback, and tune themselves as well. Servo drives that tune themselves automatically adapt to the given motor-drive-mechanism, without a decrease in performance and with little need for further fine tuning of the control loops.
Torque and Speed Considerations
Although servo motors are designed to run at high speeds, they can accurately run at extremely low speeds under very precise control, even down to 1 rpm and below with proper preparation. When properly utilized, steppers are accurate and are usually a more economical solution for low-speed applications (less than 1,000 rpm). However, above 1,000 rpm, a stepper motor’s torque begins to fall off, the result of magnetic circuit time constants and core losses.
In contrast, servo motors with comparable torque do not start to fall off until around 2,000 to 4,000 rpm or more (Figure B). Direct-drive servo applications powering high-inertia loads are typically found utilizing speeds < 1000 rpm, while typical servo applications with a mechanically advantaged drive train are likely to be found using any speed within its working envelope of capability.
With a required speed range between 1,000 to 3,000 rpm, the motor type that should be used may be determined by such application requirements as horsepower, peak torque at speed, continuous (RMS) torque and repeatability.
At stall (low speeds < 50 steps/second or 15 rpm) or when holding a load with no movement, stepper motors, especially with oversized rotors, can produce more torque than servos for a given frame size (although newer servo motor designs are encroaching on this). All that torque lets steppers produce extremely accurate and stiff low-speed motion without a gearbox or other mechanical advantage. In contrast, Direct Drive servo motors with higher pole count and high resolution feedback are often utilized for industrial process applications requiring typical velocities of less than 1000 rpm without a mechanical advantage such as a gear head. When a stepper motor is at rest, it uses continuous energy and there is absolutely no movement (unless overloaded), and when not powered its detent torque capability can be used to hold position.
In contrast, a servo motor is never at rest when ON, due to the constant closed loop error correction, while only using the energy required to maintain its commanded position. The constantly varying position loop error causes the servo’s output shaft to move back-and-forth (though it should not be noticeable), while continuously looking for minimum error. This continuous back-and-forth actuator motion is called, hunting, similar to another term, dither, a purposely induced actuator movement (e.g. valve to continuously overcome the issues of stiction). The physical displacement during hunting, typically involves only a few feedback counts, relative to the total resolution: what is unnoticeable in most applications, can be unacceptable in others (higher resolution feedback devices reduce the typical hunting delta).
Where repeatability and resolution are an issue, traditionally servo motor territory, steppers may now be considered. For steppers, the requirement is that the load must be predictable, or subject to only small external forces and disturbances, where tight coordination between axes is not required. Steppers, running open loop, can save an initial machine cost of greater than 20-30% over comparable servo solutions.
Torque Performance
Regarding torque, designers should select the motor that provides the higher value at the speeds required, from comparable speed-torque curves. For the same price, most designers prefer to use servo motors. For constant or variable loads, servo systems can recover from overload conditions where stepper systems cannot. Steppers give a lot of torque in a small package, under 1,000 rpm. In contrast, servo motors can handle torque requirements below and well above 1,000 rpm.
Accuracy and Resolution
Stepper systems have a difference between their theoretical and actual resolution. For example, a two phase, full stepping, 1.8° step-angle motor may have 200 possible positions in one revolution (360°/1.8°), but whether or not it’s achieved depends on how the motor was sized for the application. The same is true of half stepping and micro stepping motor drive modes. A 1.8° microstepper, though specified as having ten microsteps per each full step, cannot necessarily find any position within 0.18°.
Additionally, several commanded microsteps may be required before there is enough torque build-up to overcome friction and load inertia. In a real-world situation, the motor could easily jump one or more microsteps beyond the number commanded and stabilize there. When positioning-resolution requirements need to exceed 200 steps per revolution, steppers may utilize a feedback encoder to achieve upwards of 1000 steps/rev. Five-phase motors and microstepping motors (with caution) can also improve on the steps/rev.
Repeatability
Servo motors are extremely repeatable because they run closed loop. But steppers can be just as
repeatable in many applications, especially when running in one direction. However, when an Idle Current Reduction (ICR) mode is utilized and/or the load increases (e.g. as during direction reversal) and exceeds the capability of the stepper the situation changes. Similar to how a gearbox must take up backlash, the stepper must catch up to system command. During the first move in a new direction, motor accuracy is affected, because the stepper is overcoming inertia and friction (effects of the load). Once that happens, the system regains its specified repeatability, but it may have lost or gained actual position steps over those commanded.
Conclusion
Both technologies are a clear choice in today’s mechatronic machine designs. However, once the advantages and disadvantages of servo and stepper motor systems are clearly understood, especially relative to the process or work to be performed, the best selection for a given application becomes much clearer.
Assuming the desired process can be accomplished with either a stepper or servo motor solution, with the repeatability, accuracy and flexibility requirements, for present and future needs, the remaining considerations would likely be environment, life expectancy, operating noise, and/or energy utilization.
When specific requirements allow for either technology, one should utilize discernment and foresight, with the specific knowledge of the considered working process or job to be performed, possible future needs, and the designer’s machine experience.
This article presents an overview of different baseline capabilities for selection criteria between stepper and servo technology. A thorough understanding of these technologies will help generate the best and most efficient mechatronic designs to bring forth the full capability of a machine. Today’s digital stepper motor drives provide enhanced drive features, option flexibility, and communication protocols using advanced integrated circuits and simplified programming techniques. The same is true of servo motor systems, while higher torque density, improved electronics, algorithms, and higher feedback resolution have resulted in higher system Bandwidth (BW) capabilities, and lower initial and overall operating costs for many applications.
Stepper Motor System Overview
Stepper motors have several major advantages over servo systems. They are typically lower cost, have common NEMA mountings, offer lower torque options, require less costly cabling, and their open loop motion control component makes machine integration simplistic and provides ease-of-use to end users.
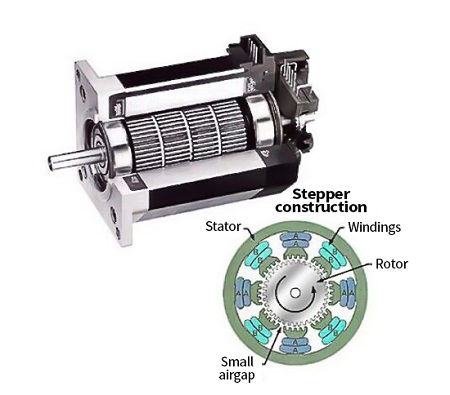
The issue of whether to use a stepper or servo is dictated by the application in most cases. Steppers are typically sized for twice their continuous requirements for additional acceleration and/or deceleration torque capability or for a required peak torque. In contrast, servo motors are generally sized for the specific application velocities and torques for maximum intermittent acceleration/deceleration, holding torque (if applicable), and continuous RMS requirements over the complete motion profile.
In general, if an application requires high-throughput, high-speed, and high-bandwidth capability for disturbance correction, and/or high-rpm, with or without tight coordination between axes, servo motors are the best option. If point-to-point position performance and rpm requirements are modest, (as a function of the process loads and expected disturbances) steppers may be a better choice. Additionally, when the loads are within reason, a stepper’s ability to hold position (using holding torque with power and detent torque without power) can be an advantage.
Speed-torque curves highlight the difference between stepper and AC permanent magnet (PM) servo motors of equal volume. Steppers typically generate higher continuous torque at lower speeds than servo motors. However, servo motors produce intermittent peak torques in this same low-speed range and produce peak and continuous torques over a much wider-higher speed range.
Automated machine axes for adjustment and setup as well as video axes for inspection, are applications that stepper systems fulfill well. Steppers are especially ideal for these type axes because they tend to be easier to design into control systems and less expensive on initial setup. When an axis for a given setup can be locked into place they are less expensive to operate (e.g. optional ON/OFF reduced power mode). Additionally, when properly applied, steppers are less prone to failure because of their simplistic open-loop control, which only requires winding-to-drive match-up versus motor-drive-to-mechanism tuning required with feedback circuits of a closed-loop system.
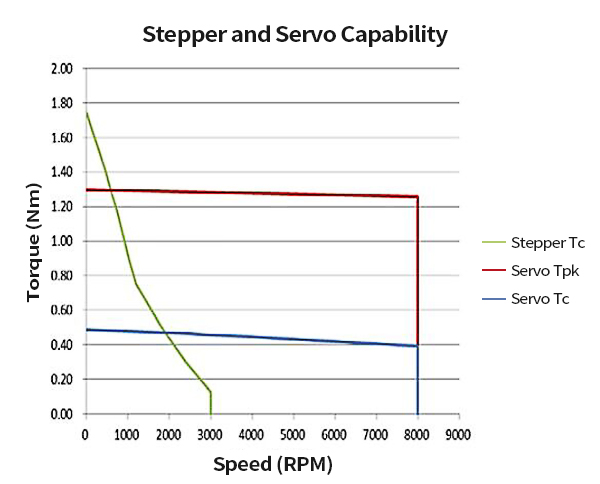
Stepper Drives
Newer design techniques have improved step motor performance by the utilization of: built-in feedback,end-of-move damping (for reduced settling times while maximizing accuracy), soft-start (to reduce jerk on power-up), anti-resonance modes (for optimizing torque, stability, and noise reduction - audible or otherwise), Idle Current Reduction (IRC - for reduced motor heating during standstill) and easily controlled operation modes between full-step, half-step and micro stepping.
Although most properly sized steppers are extremely accurate running open loop in the selected step mode, built-in feedback provides additional precision without the cost of an external feedback device. Microstepping techniques result in smoother torque and motion at low speeds and greater resolution at high speeds with the reduction of step size from full-step/half-step.
Servo Motor System Overview
Servo motors have several distinct advantages over steppers. They can generate high torque over a wide speed range on demand, and are available in wider torque ranges and higher voltages (up to 480 Vac). They respond to disturbances with a torque much greater than their continuous capability and use only the power required to accomplish the commanded motion and are compact.
Servo Drives
Motor drive compensation often referred to as tuning or comp, once considered the bane process of servo users is, for the most part, history. Today, the newest digital servo drive technologies have enhanced software and hardware capabilities for improved user experience and offer remarkable compensation flexibility. In fact, some servo systems automatically configure the motor, drive and feedback, and tune themselves as well. Servo drives that tune themselves automatically adapt to the given motor-drive-mechanism, without a decrease in performance and with little need for further fine tuning of the control loops.
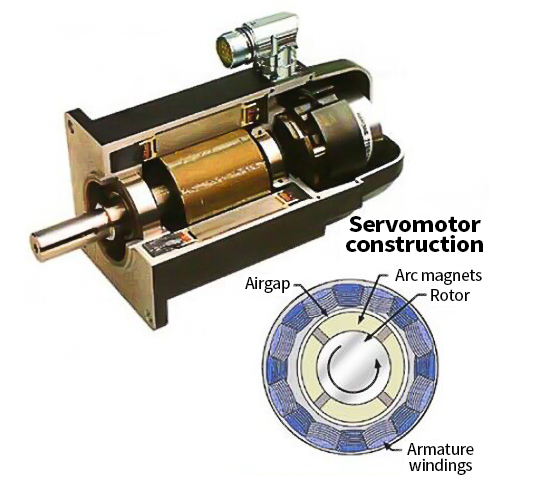
Although servo motors are designed to run at high speeds, they can accurately run at extremely low speeds under very precise control, even down to 1 rpm and below with proper preparation. When properly utilized, steppers are accurate and are usually a more economical solution for low-speed applications (less than 1,000 rpm). However, above 1,000 rpm, a stepper motor’s torque begins to fall off, the result of magnetic circuit time constants and core losses.
In contrast, servo motors with comparable torque do not start to fall off until around 2,000 to 4,000 rpm or more (Figure B). Direct-drive servo applications powering high-inertia loads are typically found utilizing speeds < 1000 rpm, while typical servo applications with a mechanically advantaged drive train are likely to be found using any speed within its working envelope of capability.
With a required speed range between 1,000 to 3,000 rpm, the motor type that should be used may be determined by such application requirements as horsepower, peak torque at speed, continuous (RMS) torque and repeatability.
At stall (low speeds < 50 steps/second or 15 rpm) or when holding a load with no movement, stepper motors, especially with oversized rotors, can produce more torque than servos for a given frame size (although newer servo motor designs are encroaching on this). All that torque lets steppers produce extremely accurate and stiff low-speed motion without a gearbox or other mechanical advantage. In contrast, Direct Drive servo motors with higher pole count and high resolution feedback are often utilized for industrial process applications requiring typical velocities of less than 1000 rpm without a mechanical advantage such as a gear head. When a stepper motor is at rest, it uses continuous energy and there is absolutely no movement (unless overloaded), and when not powered its detent torque capability can be used to hold position.
In contrast, a servo motor is never at rest when ON, due to the constant closed loop error correction, while only using the energy required to maintain its commanded position. The constantly varying position loop error causes the servo’s output shaft to move back-and-forth (though it should not be noticeable), while continuously looking for minimum error. This continuous back-and-forth actuator motion is called, hunting, similar to another term, dither, a purposely induced actuator movement (e.g. valve to continuously overcome the issues of stiction). The physical displacement during hunting, typically involves only a few feedback counts, relative to the total resolution: what is unnoticeable in most applications, can be unacceptable in others (higher resolution feedback devices reduce the typical hunting delta).
Where repeatability and resolution are an issue, traditionally servo motor territory, steppers may now be considered. For steppers, the requirement is that the load must be predictable, or subject to only small external forces and disturbances, where tight coordination between axes is not required. Steppers, running open loop, can save an initial machine cost of greater than 20-30% over comparable servo solutions.
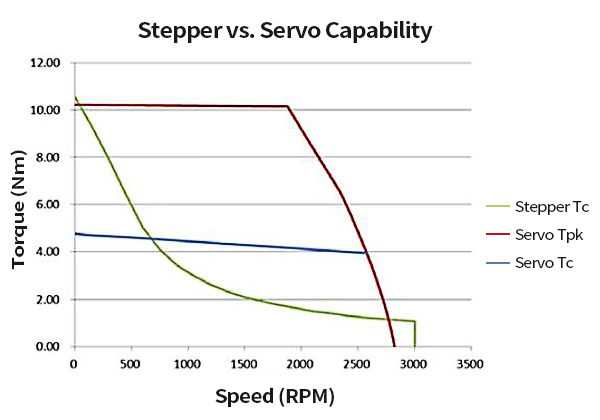
Regarding torque, designers should select the motor that provides the higher value at the speeds required, from comparable speed-torque curves. For the same price, most designers prefer to use servo motors. For constant or variable loads, servo systems can recover from overload conditions where stepper systems cannot. Steppers give a lot of torque in a small package, under 1,000 rpm. In contrast, servo motors can handle torque requirements below and well above 1,000 rpm.
Accuracy and Resolution
Stepper systems have a difference between their theoretical and actual resolution. For example, a two phase, full stepping, 1.8° step-angle motor may have 200 possible positions in one revolution (360°/1.8°), but whether or not it’s achieved depends on how the motor was sized for the application. The same is true of half stepping and micro stepping motor drive modes. A 1.8° microstepper, though specified as having ten microsteps per each full step, cannot necessarily find any position within 0.18°.
Additionally, several commanded microsteps may be required before there is enough torque build-up to overcome friction and load inertia. In a real-world situation, the motor could easily jump one or more microsteps beyond the number commanded and stabilize there. When positioning-resolution requirements need to exceed 200 steps per revolution, steppers may utilize a feedback encoder to achieve upwards of 1000 steps/rev. Five-phase motors and microstepping motors (with caution) can also improve on the steps/rev.
Repeatability
Servo motors are extremely repeatable because they run closed loop. But steppers can be just as
repeatable in many applications, especially when running in one direction. However, when an Idle Current Reduction (ICR) mode is utilized and/or the load increases (e.g. as during direction reversal) and exceeds the capability of the stepper the situation changes. Similar to how a gearbox must take up backlash, the stepper must catch up to system command. During the first move in a new direction, motor accuracy is affected, because the stepper is overcoming inertia and friction (effects of the load). Once that happens, the system regains its specified repeatability, but it may have lost or gained actual position steps over those commanded.
Conclusion
Both technologies are a clear choice in today’s mechatronic machine designs. However, once the advantages and disadvantages of servo and stepper motor systems are clearly understood, especially relative to the process or work to be performed, the best selection for a given application becomes much clearer.
Assuming the desired process can be accomplished with either a stepper or servo motor solution, with the repeatability, accuracy and flexibility requirements, for present and future needs, the remaining considerations would likely be environment, life expectancy, operating noise, and/or energy utilization.
When specific requirements allow for either technology, one should utilize discernment and foresight, with the specific knowledge of the considered working process or job to be performed, possible future needs, and the designer’s machine experience.
Post a Comment:
You may also like:
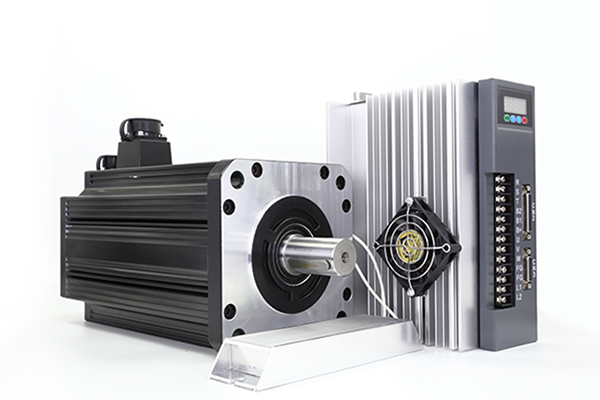
Category
Featured Articles
What is a Servo Motor?
There are some special types of application of electrical motor where rotation of the motor is required for just a certain angle ...
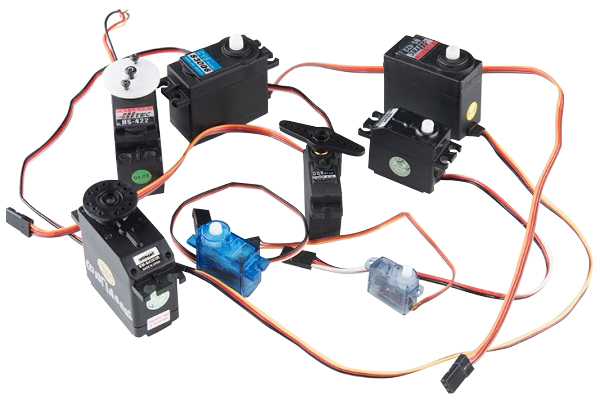
How to Select the Suitable Power ...
It's important to consider the unique demands of a motion control application when selecting a power supply. During ...
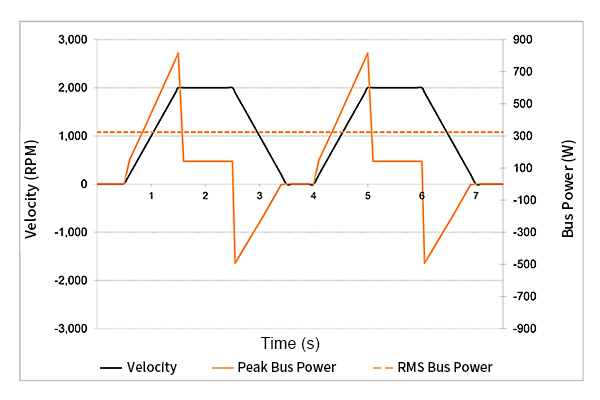
What are the Types of Servo Motor?
There are some special types of application of electrical motor where rotation of the motor is required for just a certain angle ...
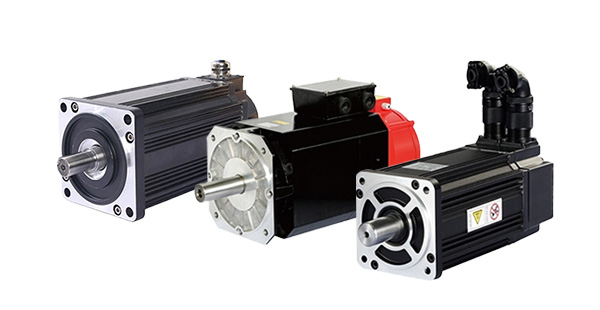
How to Maintain Servo Motor?
Servo motors play a crucial role in various industries, serving as precision control devices in applications ranging from ...
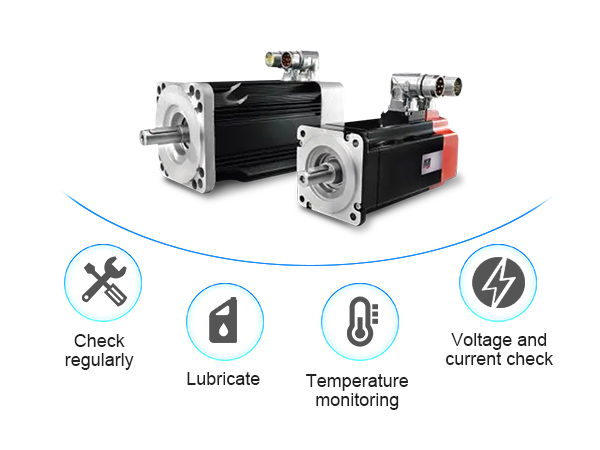
How to Test Servo Motor?
Servo motors are devices that convert electrical signals into mechanical motion and are widely used in industrial automation, ...
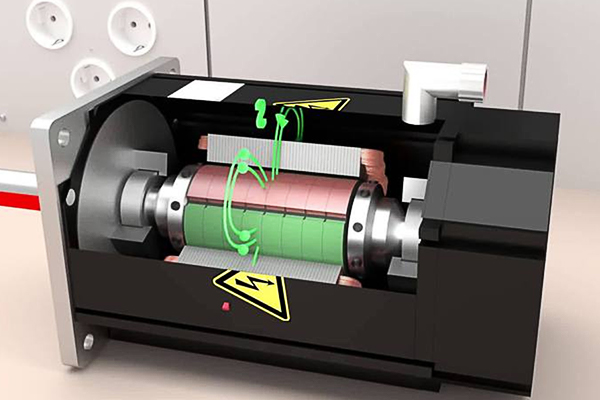