How to Select the Suitable Power Supply For Servo Motor Application?
It's important to consider the unique demands of a motion control application when selecting a power supply. During accelerations, motor drives can quickly draw large amounts of power. Additionally, motors can create regenerative energy and push current back into the power supply during deceleration, which means the power supply needs to handle the resulting increase in voltage. Highly dynamic motion applications place large and rapid demands for current on the power supply.
There are many other important factors to consider when choosing the best power supply that are not specifically related to motion control. Some of these considerations are especially important to OEM machine designers looking to minimize the cost of their product and provide reliable operation over a wide variety of operating conditions.
Peak Power
A pumping application which generally runs at a fixed or slowly varying speed and torque, uses a peak power fairly close to its average (continuous) power. A pick & place machine on the other hand, with lots of starts and stops at high acceleration, has a much higher peak than average power demand.
For a well-designed system, you'll need to consider the peak and average power draw for all axes combined (which, usually, is not simply the sum of the individual axes' requirements). A multi-axis machine with axes that have overlapping motion profiles (i.e. the axes may accelerate at the same time) will likely require much more peak power than machines where only one axis moves at a time.
The graph below displays the velocity during a typical "trapezoidal" move versus both the peak and average (RMS) power (in Watts).
The RMS average power demand for this repeating move is about 323 watts. However, the peak power is over 800 watts or more than 2.5x the RMS power requirement. You can see why it’s important to select a power supply for both the peak as well as the average demand.
DC Output Voltage Level
This is a trickier question than it appears at first glance. Assuming you want the lowest overall cost for the mechanical power your application needs, and that you are using motors in the 100 watt to 750 watt range (fractional horsepower), there is a sweet spot around 65-85 volts DC.
Many people want to use a 24 volt power supply because these supplies are very easy to find, or because their application already needs 24 volts (for sensors and other components). Many power motors, including most of Teknic's motors, can be run from a 24 volt supply, so why not use 24 volts?
The main reason is that increasing the motor's supplied bus voltage (to a point) is the lowest cost way of getting more motor power. The mechanical power from the sha of a motor at any given speed is the speed multiplied by the torque. The maximum speed of any motor is directly related to its supplied voltage. The amount of torque you can get from a motor is proportional to the current you push through its windings, which in turn, is also limited by the power supply voltage. So, the way to get the most power out of any given motor (speed x torque), is to increase its supplied voltage.
Additionally, for any given voltage, a motor will spin faster if the motor's stator coils have fewer turns of copper wire. And with fewer turns, you can use heavier gauge wire, which will have lower resistance and provide more current per volt. So, why not use a motor with fewer stator coil turns and use a lower power supply voltage?
You can, to a point, but there are tradeoffs. Resistive losses in the drive and the power supply are proportional to the square of the current, so as the current goes up, the drive and power supply have to dissipate a disproportionate amount of heat. Additionally, it's harder to pack copper wire into a motor stator when you're using relatively few turns of large diameter wire compared to when you’re using more turns of small diameter wire (as an analogy, think of the amount of wasted space in a jar filled with rocks versus one filled with sand). Less copper fill for any given motor geometry means less motor power.
Conversely, why not use really high voltage? Again, tradeoffs. For motors larger than 1-2 horsepower, it would be impractical not to use high voltage. But for fractional horsepower motors, the use of high voltage brings a number of safety and regulatory issues that increase project complexity and increase cost. When using a supply in the 75 VDC range, the current required to achieve motor power up to 1-2 horsepower is not high enough to worry about the resistive losses and copper fill issues described above. And at 75 VDC, it's pretty easy and inexpensive to meet electrical safety regulations.
Below is an example of the torque/speed curves for the same servo motor system powered from three different DC voltages: 24V, 48V, and 75V:
You can see from the torque/speed graphs and from the summary table below, that there is a significant difference in mechanical shaft power that you can get from the same motor just by increasing the supply voltage. Note that, at 24 VDC, the motor doesn't have enough voltage to achieve the peak torque (815 oz-in) that is possible at 48 and 75 VDC.
Depending on your exact requirements, you might be able to use a lower than optimal voltage and still get the mechanical power you need. That said, to do so, you'll probably have to use a larger and more expensive motor than you'd otherwise need. In our website, we will provide professional solutions for your servo motor application.
There are many other important factors to consider when choosing the best power supply that are not specifically related to motion control. Some of these considerations are especially important to OEM machine designers looking to minimize the cost of their product and provide reliable operation over a wide variety of operating conditions.
Peak Power
A pumping application which generally runs at a fixed or slowly varying speed and torque, uses a peak power fairly close to its average (continuous) power. A pick & place machine on the other hand, with lots of starts and stops at high acceleration, has a much higher peak than average power demand.
For a well-designed system, you'll need to consider the peak and average power draw for all axes combined (which, usually, is not simply the sum of the individual axes' requirements). A multi-axis machine with axes that have overlapping motion profiles (i.e. the axes may accelerate at the same time) will likely require much more peak power than machines where only one axis moves at a time.
The graph below displays the velocity during a typical "trapezoidal" move versus both the peak and average (RMS) power (in Watts).
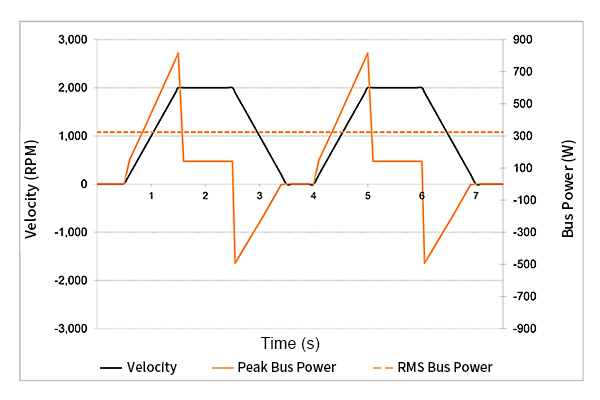
The RMS average power demand for this repeating move is about 323 watts. However, the peak power is over 800 watts or more than 2.5x the RMS power requirement. You can see why it’s important to select a power supply for both the peak as well as the average demand.
DC Output Voltage Level
This is a trickier question than it appears at first glance. Assuming you want the lowest overall cost for the mechanical power your application needs, and that you are using motors in the 100 watt to 750 watt range (fractional horsepower), there is a sweet spot around 65-85 volts DC.
Many people want to use a 24 volt power supply because these supplies are very easy to find, or because their application already needs 24 volts (for sensors and other components). Many power motors, including most of Teknic's motors, can be run from a 24 volt supply, so why not use 24 volts?
The main reason is that increasing the motor's supplied bus voltage (to a point) is the lowest cost way of getting more motor power. The mechanical power from the sha of a motor at any given speed is the speed multiplied by the torque. The maximum speed of any motor is directly related to its supplied voltage. The amount of torque you can get from a motor is proportional to the current you push through its windings, which in turn, is also limited by the power supply voltage. So, the way to get the most power out of any given motor (speed x torque), is to increase its supplied voltage.
Additionally, for any given voltage, a motor will spin faster if the motor's stator coils have fewer turns of copper wire. And with fewer turns, you can use heavier gauge wire, which will have lower resistance and provide more current per volt. So, why not use a motor with fewer stator coil turns and use a lower power supply voltage?
You can, to a point, but there are tradeoffs. Resistive losses in the drive and the power supply are proportional to the square of the current, so as the current goes up, the drive and power supply have to dissipate a disproportionate amount of heat. Additionally, it's harder to pack copper wire into a motor stator when you're using relatively few turns of large diameter wire compared to when you’re using more turns of small diameter wire (as an analogy, think of the amount of wasted space in a jar filled with rocks versus one filled with sand). Less copper fill for any given motor geometry means less motor power.
Conversely, why not use really high voltage? Again, tradeoffs. For motors larger than 1-2 horsepower, it would be impractical not to use high voltage. But for fractional horsepower motors, the use of high voltage brings a number of safety and regulatory issues that increase project complexity and increase cost. When using a supply in the 75 VDC range, the current required to achieve motor power up to 1-2 horsepower is not high enough to worry about the resistive losses and copper fill issues described above. And at 75 VDC, it's pretty easy and inexpensive to meet electrical safety regulations.
Below is an example of the torque/speed curves for the same servo motor system powered from three different DC voltages: 24V, 48V, and 75V:
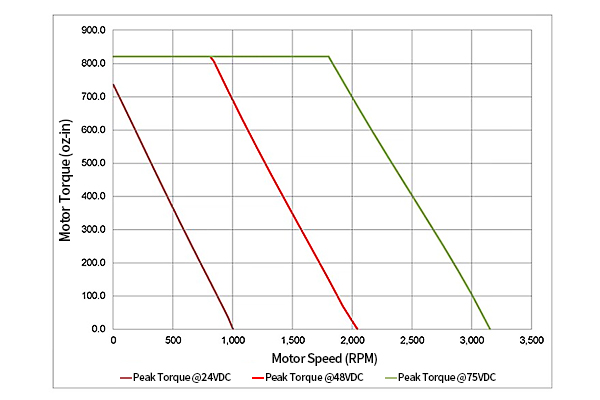
You can see from the torque/speed graphs and from the summary table below, that there is a significant difference in mechanical shaft power that you can get from the same motor just by increasing the supply voltage. Note that, at 24 VDC, the motor doesn't have enough voltage to achieve the peak torque (815 oz-in) that is possible at 48 and 75 VDC.
Depending on your exact requirements, you might be able to use a lower than optimal voltage and still get the mechanical power you need. That said, to do so, you'll probably have to use a larger and more expensive motor than you'd otherwise need. In our website, we will provide professional solutions for your servo motor application.
Post a Comment:
You may also like:
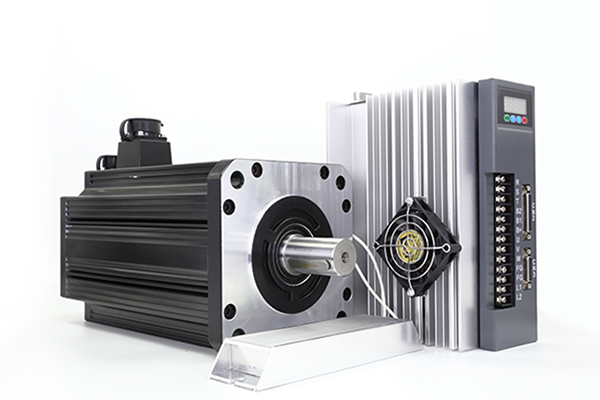
Category
Featured Articles
What is a Servo Motor?
There are some special types of application of electrical motor where rotation of the motor is required for just a certain angle ...
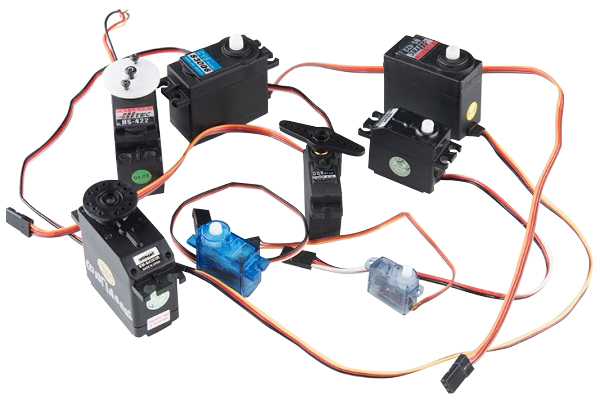
How to Test Servo Motor?
Servo motors are devices that convert electrical signals into mechanical motion and are widely used in industrial automation, ...
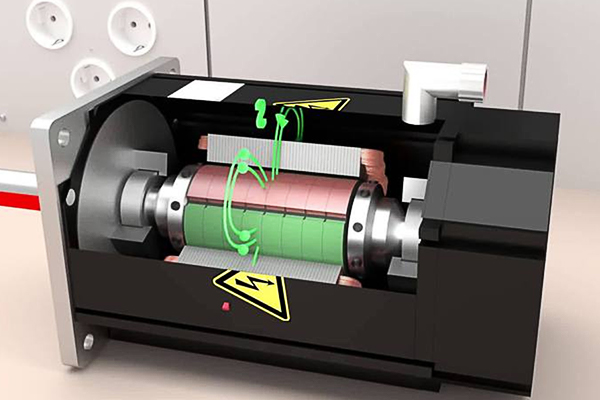
How to Maintain Servo Motor?
Servo motors play a crucial role in various industries, serving as precision control devices in applications ranging from ...
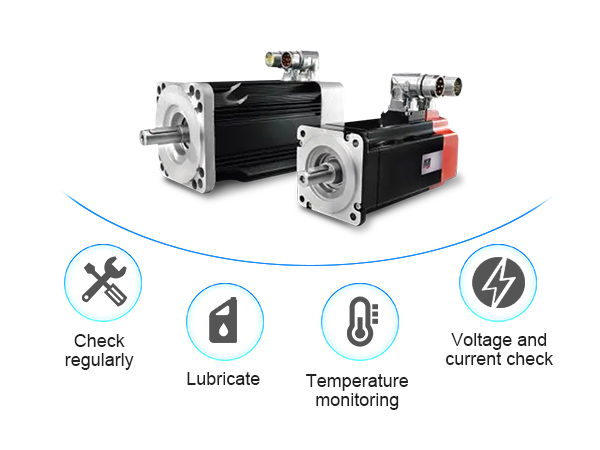
What are the Types of Servo Motor?
There are some special types of application of electrical motor where rotation of the motor is required for just a certain angle ...
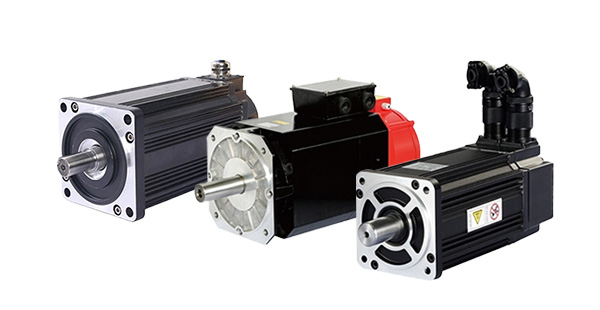
How to Select the Suitable Power ...
It's important to consider the unique demands of a motion control application when selecting a power supply. During ...
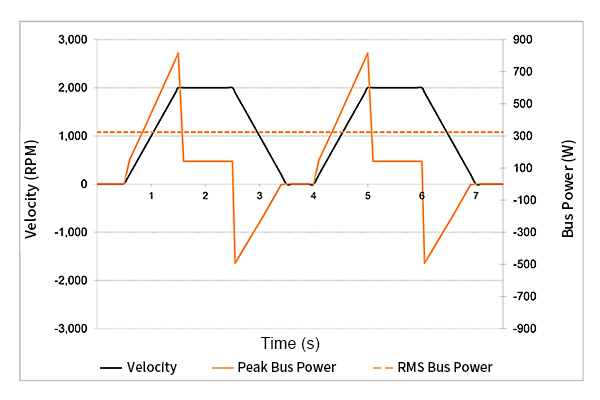