Home » Servo Drive » How to Control Position Accuracy of Servo Drive?
How to Control Position Accuracy of Servo Drive?
Factors affecting servo drive positioning
Servo drive to achieve high-precision positioning mainly depends on its closed-loop control system and related technology. The following are some key points.
Servo drive to achieve high-precision positioning mainly depends on its closed-loop control system and related technology. The following are some key points.
- Encoder feedback: servo motors are equipped with high-resolution encoder, which can provide real-time position and speed of the motor feedback.
- Controller algorithms: The micro controller in the servo drive adjusts the motor's input voltage or current according to the encoder feedback and controller algorithms to control the motor's speed and position.
-
Current and speed closed-loop control:
servo drive with current and speed closed-loop control, can quickly respond to
speed changes or load disturbances, to ensure that the motor to run in the best
state.
-
Position control: through the controller
algorithm, the servo drive can accurately control the position of the motor,
even in complex trajectories or rapid positioning applications can also
maintain high accuracy.
-
Rigidity: the rigidity of the servo drive and motor system determines its resistance to external disturbances (such as
load changes). High rigidity can ensure that in high-precision positioning
applications, even in external interference, the system can remain stable.
-
Control strategy: servo drive can use a
variety of advanced control strategies, such as adaptive control, fuzzy
control, in order to improve the dynamic performance of the system and
positioning accuracy.
-
Temperature compensation: servo drive
usually has a temperature compensation function to reduce the motor due to
temperature changes and thermal errors, further improve positioning accuracy.
These technologies and methods work
together to enable the servo drive to achieve high-precision positioning. It
should be noted that the actual application of the accuracy will be affected by
other factors, such as mechanical systems, control parameter settings,
environmental conditions. Therefore, in the use of servo drives for
high-precision positioning, but also need to carry out a comprehensive system
analysis and debugging.
Some method to control the accuracy
Servo drives can be used in a variety of ways to improve positioning accuracy, the following are some common methods.
- Optimize the servo system parameters: servo system parameters include proportional gain, integral time constant and differential time constant. Proportional gain is the servo system output and error ratio. Set a reasonable proportional gain can effectively improve the positioning accuracy of the servo system. However, too high proportional. Gain can also lead to excessive oscillation, thus affecting the performance of the system. In determining the servo system parameters, careful adjustment and optimization is required to find the best parameter configuration.
- Improve the resolution of the encoder: increase the size of the grating piece and the number of bits, increase the sampling frequency of the encoder is a common way to improve the resolution of the encoder. Resolution of the encoder can provide more accurate position information, thereby improving the positioning accuracy of the servo system.
- Reduce mechanical clearance: mechanical clearance is one of the key factors affecting positioning accuracy. Mechanical clearance is divided into two categories of drive system clearance and system rigidity clearance. In practical applications, should be adjusted through the tightness of the transmission parts, optimize the design of the transmission system, as much as possible to reduce the mechanical gap, improve the positioning accuracy of the servo system.
- Improve the response speed of the servo controller: the response speed of the servo controller will also affect the positioning accuracy. Improve the processing speed of the controller and the optimization of the algorithm can reduce the control delay, improve the response speed of the system, thereby improving the positioning accuracy.
- Introduction of advanced control strategies: some advanced control strategies, such as adaptive control, fuzzy control, etc., can help improve the positioning accuracy of the servo system. These strategies can be adjusted according to the real-time state of the system and external disturbances to achieve more accurate control.
- Temperature compensation: As temperature changes may lead to servo system components of the physical changes, which in turn affects the positioning accuracy, so some advanced servo drive with temperature compensation function. This function can reduce or eliminate thermal errors caused by temperature changes, thereby improving positioning accuracy.
Post a Comment:
You may also like:
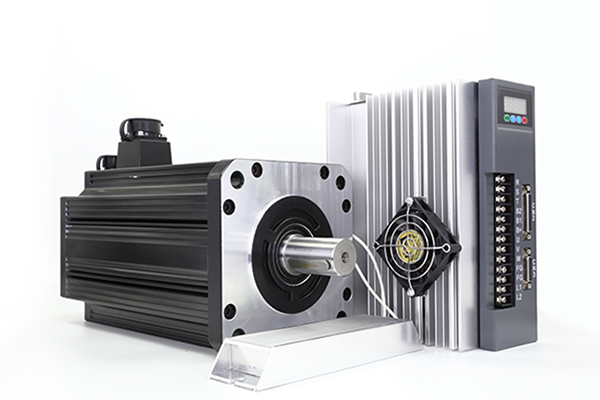
Category
Featured Articles
What are the Basics of Servo Drive?
Servo motors come in so many types and flavors that it is difficult to define them in a way that is accurate and universally ...
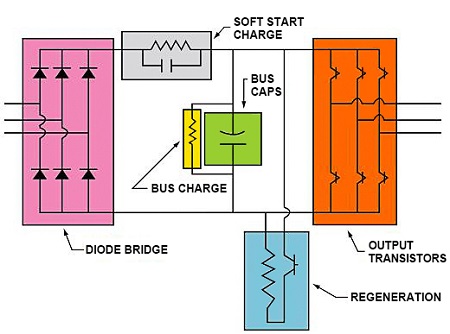
How to Install a Servo Drive?
Installing a servo drive involves several steps, and the specific process may vary depending on the manufacturer and model of the ...
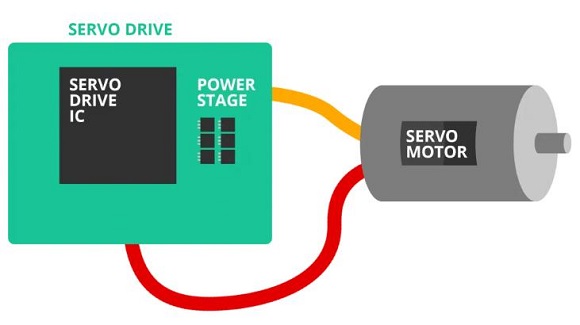
What are the Soft Start Techniques for ...
Servos (as commonly used in radio-controlled vehicles and small-scale robotics)are DC actuators that use a potentiometer to ...
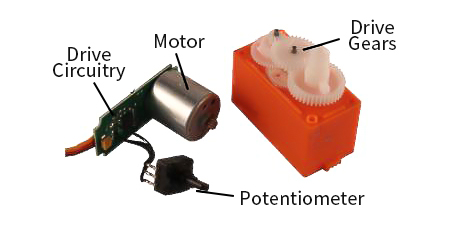
Servo Drive System vs. Variable ...
A servo drive system, as opposed to a variable frequency drive (VFD) or AC motor drive , has the ability to position with ...
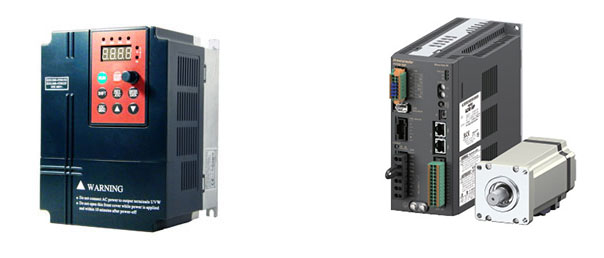